Spis treści
Ściany i dachy budynków wykonane z płyt warstwowych muszą długo utrzymywać założone w projekcie parametry, m.in. wytrzymałość, izolacyjność cieplną, akustyczną czy odporność na warunki atmosferyczne – w przypadku typowych hal przynajmniej przez 25–30 lat. W odniesieniu do bardziej skomplikowanych i strategicznych obiektów (np. elektrociepłowni) wymaga się rozwiązań o dłuższej żywotności – nawet do 50 lat. Dlatego dobierając rodzaj i parametry płyt, trzeba brać pod uwagę przeznaczenie hali przemysłowej.
Odpowiednie powłoki okładzin płyt warstwowych zapewniają trwałość obiektu w trudnych warunkach, m.in. w chłodniach i mroźniach, zakładach przetwórstwa spożywczego (gdzie mają kontakt z żywnością czy niską temperaturą – nawet do –40°C), a także w obiektach zlokalizowanych na obszarach o dużym zasoleniu lub zanieczyszczeniu powietrza.
Warunki eksploatacji a ryzyko korozji
Właściwy dobór zewnętrznej powłoki okładzin płyty warstwowej do istniejących warunków otoczenia, w jakich będzie wbudowana, jest podstawą do jej bezproblemowej i długotrwałej eksploatacji, a także do zachowania gwarancji producenta. Powierzchnie płyt są narażone na działanie różnych agresywnych czynników środowiskowych, m.in. wody, mgły solnej, wilgoci, promieniowania UV, substancji chemicznych pochodzących zarówno z zewnątrz, jak i wynikających ze specyfiki użytkowania obiektu. Mogą one powodować korozję okładzin, utratę koloru lub połysku, dlatego dobierając płyty warstwowe na obudowę hali, należy wziąć pod uwagę ich odporność na korozję w odniesieniu do środowiska, w jakim będą się znajdowały przez wiele lat.
W niektórych typach obiektów, np. zakładach produkcyjnych, chemicznych, przemysłu spożywczego, mroźniach, chłodniach, magazynach żywności lub budynkach rolniczych, płyty warstwowe mogą być narażone na czynniki agresywne, które należy uwzględnić przy doborze powłok wewnętrznych okładzin płyt. Szczególne warunki panują m.in. tam, gdzie istnieje ryzyko kontaktu ze szkodliwymi substancjami chemicznymi, żrącymi, silnie agresywnym amoniakiem oraz jego pochodnymi (składnikiem odchodów zwierzęcych), agresywnymi środkami czyszczącymi. Okładziny mogą być również wystawione na działanie atmosfery kontrolowanej, obniżonej temperatury lub na bezpośredni kontakt z żywnością.
Rodzaj powłoki antykorozyjnej, chroniącej blachę stalową zastosowaną na okładzinę płyty warstwowej, dobiera się głównie według kategorii odporności na korozję na zewnątrz (od RC1 do RC5+), które zależą przede wszystkim od warunków klimatycznych panujących wewnątrz i na zewnątrz budynku, czyli kategorii korozyjności środowiska. Określenie ryzyka korodowania powierzchni okładziny wymaga uwzględnienia przede wszystkim: wilgotności otoczenia, występowania kondensacji, temperatury powietrza, intensywności promieniowania słonecznego, ekspozycji na działanie szkodliwych substancji oraz podatności na uszkodzenia mechaniczne.
Kategorie korozyjności atmosfery od C1 do CX, w zależności od agresywności środowiska wewnątrz i na zewnątrz obiektu, zostały wskazane w normie PN-EN ISO 12944. Oprócz poziomu zanieczyszczeń na korozję atmosferyczną wpływa wilgotność powietrza w danym środowisku. Trzeba pamiętać, że korozja atmosferyczna to proces, który zachodzi na powierzchni metalu w warstwie wilgoci na tyle małej, że może być niewidoczna gołym okiem. Przyspieszają go wzrost wilgotności względnej oraz kondensacja i wzrost ilości zanieczyszczeń w atmosferze.
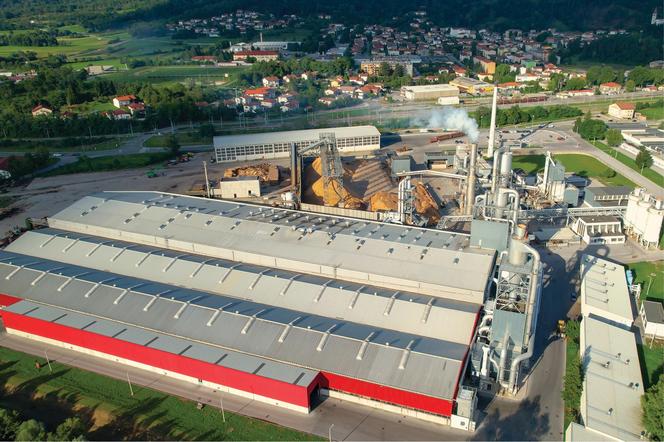
i
Wpływ promieniowania UV na trwałość powłoki
W naturalnych warunkach eksploatacji powłoki okładzin płyt warstwowych narażone są na oddziaływanie promieniowania ultrafioletowego (UV), które może powodować ich stopniową degradację. Kategorie wytrzymałości na zewnętrzne promieniowanie UV – od Ruv1 do Ruv5 – opisują, na ile powłoka zachowuje swój oryginalny kolor i połysk w warunkach zewnętrznych. Powłoki z kategorią Ruv1 charakteryzuje bardzo niska odporność, powinny więc być stosowane wyłącznie wewnątrz obiektu, zaś te z kategorią Ruv5 mają wysoką odporność na promieniowanie UV, dlatego zaleca się ich stosowanie na zewnątrz. Po ostatnich zmianach normy PN-EN 10169 pojawiła się nowa klasa Ruv5+, która stanowi obecnie najwyższą dostępną klasyfikację odporności na promieniowanie UV.
Dobierając powłokę pod względem odporności na UV, należy uwzględnić również: lokalizację geograficzną (wysokość n.p.m.), ekspozycję na słońce (północ–południe), przewidywany czas eksploatacji obiektu oraz wagę czynnika estetycznego dla danego obiektu (budynek/elewacja reprezentacyjna itp.).
Przeczytaj również:
- Płyty warstwowe na elewacji hali przemysłowej. Jak dobrać warstwowe płyty ścienne do założeń projektu?
- Jakich płyt warstwowych użyć na pokrycie dachu hali?
Rodzaje i właściwości powłok metalicznych
Grubość okładziny zewnętrznej płyt warstwowych zazwyczaj wynosi od 0,4 do 0,7 mm. Im grubsza jest blacha stalowa, tym równiej będzie wyglądała powierzchnia fasady oraz mniej odblasków będzie na niej widać przy słonecznej pogodzie. Grubość okładziny wewnętrznej zwykle wynosi od 0,4 do 0,6 mm i wpływa na długotrwałość oraz nośność płyt warstwowych. Na okładziny stosowane są zarówno blachy płaskie, jak i z drobnym profilowaniem czy też przetłoczeniami (liniowe, mikroprofilowane, faliste, rowkowe) oraz blachy o profilu sinusoidalnym.
W standardowym rozwiązaniu blacha stalowa jest powleczona obustronnie nieorganiczną metaliczną powłoką ochronną: cynkową (o gramaturze min. 225 g/m2) lub aluminiowo-cynkową, tzw. alucynkiem (o gramaturze 150–185 g/m2 i grubości 20–25 µm). Ta druga zazwyczaj jest dodatkowo zabezpieczona cienką (gr. ok. 1 µm) powłoką polimerową SPT (ang. Special Protection Treatment), która chroni również brzegi stali w kręgach oraz podnosi estetykę powierzchni.
Na rynku są również dostępne blachy powlekane specjalnymi powłokami cynkowo-aluminiowymi (95 + 5%), które po pokryciu powłoką organiczną z plastizolu (HPS200) spełniają wymagania odporności na korozję wyższe niż przewidziane w nowych kategoriach Ruv5 oraz RC5+. Produkty takie muszą pomyślnie przejść kompleksowe testy wytrzymałości na warunki atmosferyczne przez co najmniej cztery lata w środowisku o kategorii korozyjności C5.
W niektórych sytuacjach, np. gdy mamy do czynienia ze środowiskiem o wyższym stopniu agresywności, zalecane są okładziny z wysokogatunkowej specjalistycznej stali nierdzewnej, o podwyższonej odporności na korozję. Dotyczy to przede wszystkim wnętrz obiektów do przechowywania i przetwórstwa żywności, komór chłodniczych, pieczarkarni, zakładów farmaceutycznych, a także miejsc, gdzie często używa się środków myjących oraz ścierających. To bardzo drogie rozwiązanie, ale w niektórych przypadkach – jedyne możliwe.
Ciekawą alternatywą jest okładzina zewnętrzna ze stali Cor-Ten® o efektownej, charakterystycznej rdzawej barwie. Jeśli powierzchnia płyty z taką okładziną ulegnie zarysowaniu, sama się naprawia i wraca do oryginalnego wyglądu. Początkowo stal zaczyna rdzewieć jak zwykła stal węglowa, ale z czasem warstwa rdzy zamienia się w gęstą warstwę patyny uszczelniającą powierzchnię stali i uniemożliwiającą dalszą korozję. Kolor zmienia się z pomarańczowo-brązowego do jasno-, a na końcu ciemnobrązowego. Szybkość zmian i ostateczny kolor stali zależą od warunków atmosferycznych oraz jakości powietrza.
Rodzaje i właściwości powłok organicznych
Na ogół zabezpieczenie przeciwkorozyjne stalowych okładzin płyt warstwowych (górnej strony blachy – licowej) stanowią powłoki metaliczne oraz organiczna poliestrowa o grubości 25 μm. Taka ochrona jest zazwyczaj wystarczająca np. w środowiskach o średniej (C3) korozyjności atmosfery i kategorii odporności na korozję do RC3. W przypadku niestandardowych warunków środowiskowych zalecane jest zastosowanie innych grubości oraz typów powłok organicznych, które zapewnią długotrwałą, bezawaryjną eksploatację płyt warstwowych.
Zewnętrzne okładziny płyt warstwowych muszą być odporne na działanie czynników korozyjnych, m.in. wilgoci, mgły solnej, pary wodnej, deszczu, śniegu lub substancji chemicznych, a zarazem pełnić funkcję dekoracyjną.
W przypadku okładzin wewnętrznych poza odpornością na korozję muszą ponadto spełniać inne wysokie wymagania, dotyczące m.in. zapewnienia wysokiej higieny (kontakt z żywnością), odporności na niską temperaturę lub warunki atmosfery kontrolowanej, a także kontaktu z agresywnymi substancjami (w tym środkami czyszczącymi i dezynfekującymi). Istotna jest tu również grubość powłoki, która ma zagwarantować odporność na ścieranie, zadrapania stalowej okładziny oraz estetyczny wygląd i kolor powierzchni płyty.
Przy doborze powłok organicznych – poza ogólnymi cechami danego rodzaju – należy uwzględnić wiele innych, bardziej szczegółowych parametrów. Producenci często nadają powłokom własne nazwy handlowe, dlatego zawsze trzeba dokładnie sprawdzić informacje zawarte w ich kartach technicznych lub skonsultować się z producentem.
Najczęściej stosowane są powłoki organiczne nanoszone w sposób ciągły metodą coil-coating: poliestrowe, poliuretanowe, z poliflorku winylidenu oraz modyfikowanego polichlorku winylu, np. polifluorku winylu lub plastizolu.
Wśród parametrów opisujących poszczególne organiczne powłoki okładzin podawane są m.in.:
- grubość blachy, grubość i/lub gramatura powłoki, nazwy powłok metalicznych i organicznych, skład warstwy zewnętrznej i wewnętrznej;
- odporność mechaniczna: przyczepność i elastyczność powłoki, odporność na uderzenia, pękanie przy zginaniu, zarysowania oraz twardość powierzchni;odporność korozyjna:
- odporność na korozję (próba w komorze solnej), działanie wilgoci, klasa odporności korozyjnej RC,
- kategoria korozyjności atmosfery wewnętrznej lub zewnętrznej, agresywność środowiska wewnętrznego i zewnętrznego, kategoria (CPI) ochrony antykorozyjnej wewnątrz;
- odporność na temperaturę: ekspozycja ciągła, maksymalna i minimalna temperatura chwilowa;
- odporność chemiczna: adhezja, odporność na działanie kwasów i zasad;
- odporność na działanie substancji takich jak: rozpuszczalników, związki alifatyczne i alkohole, ketony, związki aromatyczne, oleje mineralne, amoniak, odporność w kontaktach z wyrobami używanymi w gospodarstwie domowym;
- kategoria odporności na promieniowanie UV;
- estetyka: wykończenie powierzchni (gładka lub struktura, np. skóra, ziarno, drewno, paski), refleksyjność/połysk, zabezpieczenie tymczasowe;
- dostępne kolory okładzin.
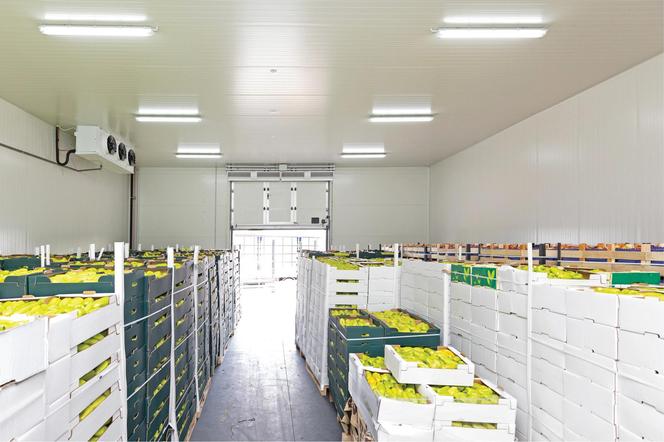
i
Wśród powłok poliestrowych można wyróżnić:
- Poliester SP 25 – grubość: 25 μm – do zastosowań zewnętrznych, 15 μm – do wewnętrznych; do użytku wewnątrz i na zewnątrz budynków; powłoka o dobrej odporności korozyjnej (RC2/RC3), na promieniowanie UV (Ruv2), zmiany temperatury i oddziaływanie czynników atmosferycznych; dostępna w wielu kolorach, ma własności dekoracyjne; do stosowania w regionach o niskiej agresywności środowiska.
- Poliester Mat – powłoka poliestrowa modyfikowana silikonem; grubość: 35 μm; dzięki grubszej warstwie lakieru i jego matowej strukturze bardziej odporna na promieniowanie UV i czynniki atmosferyczne; do stosowania wewnątrz i na zewnątrz.
- FarmCoat – modyfikowana termoutwardzalna powłoka poliestrowa; grubość: 35 μm; odporna na ścieranie, o dobrej odporności korozyjnej (RC3) i bardzo dobrej odporności chemicznej (szczególnie na amoniak); tylko do zastosowań wewnętrznych w agresywnych, wilgotnych środowiskach (C5), np. w przemyśle spożywczym i rolnictwie (magazyny zbóż, budynki inwentarskie).
- FoodCoat – specjalna powłoka lakiernicza z poliestru utwardzanego, grubość: 50 μm; dopuszczona do kontaktu z żywnością; do zastosowania w obiektach przemysłu spożywczego, np. chłodniach.
- HDS Coat (GS) – modyfikowana termoutwardzalna powłoka poliestrowo-poliuretanowa, grubość: 35 μm; o bardzo dobrej odporności korozyjnej (RC4) i na promieniowanie UV (Ruv4), stworzona do długotrwałej pracy w agresywnych środowiskach (C4).
Do najpopularniejszych powłok poliuretanowych zalicza się:
- Poliuretan PU – grubość: 50–55 μm, o wysokiej odporności na działanie wilgoci, środków chemicznych; powłoka lekko elastyczna, wyjątkowo odporna na ścieranie, zadrapania, brud oraz na uszkodzenia, na działanie promieni UV (Ruv4), o wysokiej trwałości koloru i połysku; przeznaczona do stosowania w środowiskach standardowych, agresywnych i wymagających, o bardzo wysokiej korozyjności (C5).
- Poliuretan Pural Farm – na bazie poliuretanu z dodatkiem poliamidu; grubość: 55 μm, o bardzo wysokiej odporności na korozję (RC5), zarysowania oraz na silne promieniowanie UV (Ruv4); powłoka bardzo trwała, zapewnia estetyczny i niezmienny kolor, odporna na ścieranie, zabrudzenia, częste czyszczenie, a także oddziaływanie związków chemicznych z grupy amoniaku i wodorotlenku sodu; stworzona do długotrwałej pracy w bardzo agresywnych środowiskach o korozyjności (C5); stosowana najczęściej w obiektach rolniczych.
Wśród pozostałych powłok można wyróżnić te na bazie polichlorku winylu oraz żywic m.in.:
- FOOD SAFE – folia ze zmodyfikowanego polichlorku winylu PVC(F); grubość: 120 μm (na zamówienie 150 μm); o zwiększonej twardości, nietoksyczna, chemicznie obojętna, odporna na pleśń, łatwa w czyszczeniu z użyciem większości środków myjących, dopuszczona do kontaktu z żywnością; przeznaczona do okładzin płyt stosowanych w obiektach o wysokiej wilgotności, zakładach spożywczych oraz farmaceutycznych; odporna na środowisko agresywne, m.in. działanie środków czyszczących oraz ścierających, na zadrapania i brud, przeznaczona do zastosowania wewnętrznego w obiektach przemysłu spożywczego, chłodni.
- HPS 200 – powłoka z plastizolu (PVC-P); grubość: 200 μm; o bardzo wysokiej trwałości i odporności na korozję (RC5), odporna na działanie promieni UV (Ruv4), ścieranie, zadrapania i brud; szczególnie polecana w regionach o wysokim zanieczyszczeniu przemysłowym oraz w obszarach nadmorskich; także do bardzo silnie agresywnego środowiska wewnętrznego; dostępne są okładziny z taką powłoką, które mają bardzo wysoką odporność na korozję (RC5+).
- PVD(F) – specjalistyczny fluoropolimer termoplastyczny (polifluorek winylidenu); grubość: 25 μm (2 warstwy), 35 μm (3 warstwy – dodatkowa podkładowa); powłoka o wysokiej odporności na korozję (RC4) oraz wysokiej trwałości kolorów i odporności na płowienie (zachowuje nasycenie koloru z upływem czasu); o wysokiej twardości i odporności chemicznej; odporna na uszkodzenia mechaniczne, brud.
- Fiberglass PRFV – powłoka z żywicy poliestrowej i włókien szklanych; o wysokiej odporności na chemikalia i czynniki biologiczne, przede wszystkim na opary amoniaku i uryny, występujące w budynkach inwentarskich; stosowana w środowiskach agresywnych, najczęściej jako okładzina wewnętrzna w płytach warstwowych przeznaczonych do obiektów rolniczych (np. Agro z dodatkową warstwą antykondensacyjną); można myć wodą pod ciśnieniem przy zachowaniu odpowiedniej odległości i kierunku mycia.
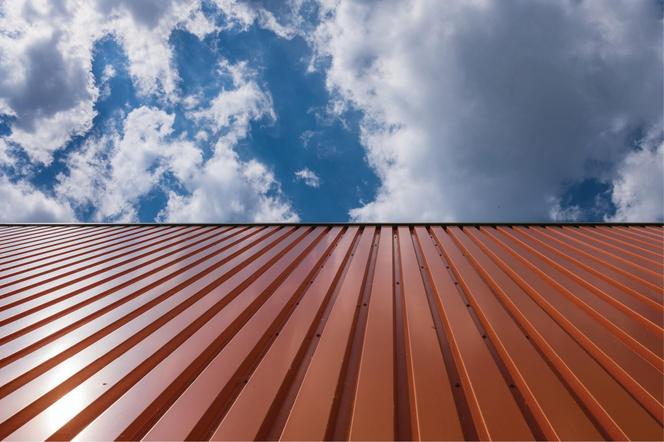
i
Kryteria doboru koloru powłoki
Podstawowa oferta płyt warstwowych zwykle obejmuje zestaw standardowych kolorów okładziny zewnętrznej i kilka jasnych odcieni okładziny wewnętrznej. U większości producentów można zamówić inne – zazwyczaj z palety RAL. Trzeba jednak pamiętać, że określa ona kolory z pewną dokładnością i tolerancją, dlatego mogą zdarzać się różnice w wyglądzie powłok klasyfikowanych jako ten sam kolor RAL, ale wykonanych z innych materiałów. Poza tym przykłady podawane w katalogach nie zawsze idealnie oddają odcień.
Z kolei w przypadku dobudowy części obiektu z wykorzystaniem nowo zamówionych płyt (nawet od tego samego dostawcy), różnica w odcieniu może być widoczna, ponieważ istniejąca elewacja pod wpływem UV może tracić kolor i połysk.
Powłoki często wpływają również na wygląd elewacji. Mogą mieć fakturę gładką lub ziarnistą oraz w różnym stopniu pochłaniać lub odbijać światło, a tym samym wywoływać różne efekty optyczne – zależnie od profilowania blachy. Ponadto np. obrót o 180° elementu z okładziną w kolorze metalicznym powoduje zmianę efektu wizualnego. Podczas montażu płyt w okładzinach kolorowych należy też na bieżąco dokonywać kontroli barwy na elewacji.
Wpływ koloru okładziny na obciążenia termiczne
W normie PN-EN 14509 kolory stosowane na okładzinach zewnętrznych płyt podzielono na trzy grupy: bardzo jasne (I), jasne (II) i ciemne (III), w związku z wpływem obciążeń termicznych na obudowy wykonane z płyt warstwowych. Minimalna wartość temperatury okładziny zewnętrznej (dla obliczeń stanu nośności i odpowiednia dla obliczeń stanu granicznego użytkowania) przyjmowana jest w zależności od tego, do której grupy przypisany jest dany kolor, i wynosi odpowiednio: 55°C dla bardzo jasnych, 65°C dla jasnych i 80°C dla ciemnych.
Płyta warstwowa, na skutek różnicy temperatur wewnątrz i na zewnątrz obiektu, poddawana jest niekorzystnym zjawiskom – stal mocniej się rozszerza lub kurczy niż rdzeń. Różnica w rozszerzalności stali i rdzenia rośnie wraz ze wzrostem temperatury powierzchni, co wiąże się ze stopniem absorpcji promieniowania, czyli z kolorem. Jest to bardzo istotne przy kolorach ciemnych i bardzo ciemnych, gdy wpływ temperatury jest znaczący i trzeba go sumować z innymi obciążeniami podczas projektowania obiektu. Na skutek dużej różnicy temperatur pomiędzy okładziną zewnętrzną a wewnętrzną powstają naprężenia termiczne, które mogą spowodować pofalowanie powierzchni lub w skrajnych przypadkach zniszczenie płyty na podporze pośredniej. Dlatego zaleca się ograniczać długości pojedynczych płyt lub nawet eliminować kolory ciemne i zastępować je jaśniejszymi.
Większość producentów ma swoje wewnętrzne ustalenia, np. co do dozwolonej długości płyt warstwowych z okładziną zewnętrzną w ciemnym kolorze. W przypadku elewacji zwykle zalecanym schematem statycznym jest układ jednoprzęsłowy, zwłaszcza w przypadku płyt o gładkiej, nieprofilowanej powierzchni. Ponadto należy stosować odpowiednie dylatacje, mocowania oraz uwzględniać wpływ temperatury montażu na deformacje okładziny (montaż w temp. >10°C).
Z kolei do płyt dachowych, które zwykle silnie się nagrzewają, zaleca się stosować okładziny w bardzo jasnym kolorze – najlepiej białym. Może się jednak zdarzyć, że w bardzo zanieczyszczonym środowisku będą się na nich gromadzić silne zabrudzenia, które spowodują zmianę koloru na ciemny i zwiększą ryzyko znacznego wzrostu temperatury okładziny.
Podczas projektowania obudowy z płyt warstwowych należy korzystać z opracowywanych przez producentów płyt tablic nośności wyrobów, które określają m.in. parametry nośności i użytkowe dla ustalonych wartości różnic temperatury między okładzinami lub przez rozróżnienie wymienionych grup kolorystycznych. Ewentualną zmianę koloru płyty trzeba uzgadniać z projektantem, ponieważ odcień powłoki ma znaczenie podczas obliczeń konstrukcyjnych.
Ryzyko uszkodzenia powłoki
Płyty warstwowe pokryte są fabrycznie jedno- lub dwustronnie folią, która chroni je przed uszkodzeniem w czasie produkcji, transportu i montażu. Po zamontowaniu płyt należy ją zdjąć w terminie podanym przez producenta (zwykle 30 lub 60 dni od daty produkcji), w przeciwnym razie może się zwulkanizować z blachą, co uniemożliwi jej usunięcie.
W trakcie nawet najbardziej starannie przeprowadzonego procesu produkcyjnego, transportu, załadunku, rozładunku czy przycinania płyt na budowie może dojść do niewielkich uszkodzeń powierzchni. Przed montażem płyt należy dokładnie ocenić ich jakość oraz stan powłoki organicznej, a ewentualne wady i uszkodzenia zgłosić producentowi.
Należy pamiętać, że montaż płyt warstwowych powinien odbywać się temperaturze otoczenia od –5 do 20°C (w przypadku tych z okładzinami w kolorach ciemnych – powyżej 10°C), a prace związane z uszczelnianiem – w nie niższej niż 4°C.
Podstawowe narzędzia potrzebne do montażu płyt warstwowych to m.in.: wkrętarka z regulowaną mocą dokręcania, wyposażona w odpowiednią głowicę do prowadzenia długich łączników, ogranicznik głębokości osadzania, nakładkę uniemożliwiającą przekręcenie wkrętów i wgniecenie powierzchni płyt, ssawkowy zestaw do transportu i montażu płyt. Do przycinania płyt zaleca się stosowanie pilarek o drobnozębnych brzeszczotach lub specjalistycznych pił tarczowych do zimnego cięcia płyt, a do obróbek blacharskich – nożyc ręcznych. Nie wolno używać szlifierek kątowych ani innych narzędzi ciernych, podgrzewających okładziny w trakcie cięcia, ponieważ uszkodzenie powłok ochronnych może stworzyć ognisko korozji, a w przypadku rdzenia styropianowego przypadkowa iskra może spowodować samozapłon materiału izolacyjnego.
Przyczyną uszkodzenia nawet najlepiej dobranej, wysokiej jakości powłoki, które niesie ryzyko pojawienia się korozji, mogą być także m.in.:
- korozja elektrochemiczna spowodowana kontaktem metali o różnej czynności elektrochemicznej;
- obecność niechronionych krawędzi cięcia;
- nieusunięcie metalowych odpadów i opiłków po obróbce i zamontowaniu płyt;
- stosowanie nieodpowiednich łączników lub akcesoriów;
- nieprawidłowa eksploatacja, brak regularnych przeglądów okładzin, ew. źle wykonana naprawa usterki;
- mycie i czyszczenie powierzchni płyt za pomocą środków, które mogą odbarwiać powłokę oraz wykonywanie tych prac w obniżonej temperaturze;
- nieostrożne odśnieżanie dachu przy użyciu ostrych narzędzi i w nieodpowiednim obuwiu.
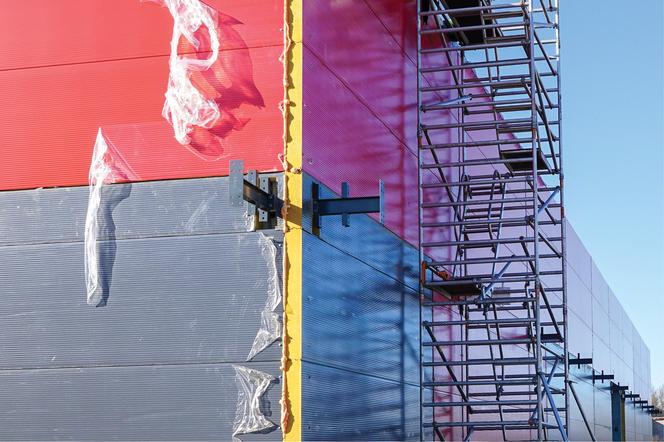
i
Podsumowanie
W każdym przypadku należy indywidualnie rozpatrywać projekt obudowy obiektu oraz dobierać rodzaj i kolor powłoki okładziny płyt warstwowych. Trzeba przy tym, poza rodzajem i przeznaczeniem obiektu, uwzględnić zarówno odpowiednie normy, badania laboratoryjne, jak i warunki klimatyczne terenu, na którym ma być wybudowana hala. Należy brać pod uwagę kilka różnych norm (m.in. dotyczących całych płyt, a także okładzin, stali oraz powłok, szczegółowych kryteriów doboru czy sposobu badań), które nie zawsze są ze sobą w sposób oczywisty powiązane.
Ponadto w ostatnich latach wprowadzono w nich wiele zmian, dlatego nie bez znaczenia jest również bezpośrednia konsultacja z producentem konkretnych płyt warstwowych. Lepiej rozwiać wcześniej wszelkie wątpliwości, ponieważ niezastosowanie się do wytycznych zalecanych przy projektowaniu obiektu i doborze parametrów płyt może skutkować pojawieniem się odkształceń powierzchni na płytach oraz miejscową utratą stateczności, za co producent płyt nie bierze odpowiedzialności.