Spis treści
Zawilgocenie hali przemysłowej – trudny problem
Konieczność stosowania zabezpieczeń wodochronnych wynika wprost z przepisów zawartych w „Warunkach technicznych, jakim powinny odpowiadać budynki i ich usytuowanie” (DzU z 2022 r., poz. 1225)):
- § 309. Budynek powinien być zaprojektowany i wykonany z takich materiałów i wyrobów oraz w taki sposób, aby nie stanowił zagrożenia dla higieny i zdrowia użytkowników lub sąsiadów, w szczególności w wyniku: (...) 6) występowania wilgoci w elementach budowlanych lub na ich powierzchniach;
- § 316 ust. 1. Budynek posadowiony na gruncie, na którym poziom wód gruntowych może powodować przenikanie wody do pomieszczeń, należy zabezpieczyć za pomocą drenażu zewnętrznego lub w inny sposób przed infiltracją wody do wnętrza oraz zawilgoceniem;
- § 317 ust. 1. Ściany piwnic budynku oraz stykające się z gruntem inne elementy budynku, wykonane z materiałów podciągających wodę kapilarnie, powinny być zabezpieczone odpowiednią izolacją przeciwwilgociową.
Zalecenia te dotyczą wilgoci lub wody znajdującej się w gruncie.
Jednak kwestia ryzyka zawilgocenia jest w rzeczywistości bardziej skomplikowana. Na podłogę może oddziaływać także woda od strony posadzki (niekiedy z agresywnymi mediami). Zachodzi wówczas konieczność stosowania rozwiązań zabezpieczających warstwy podłogi przed zawilgoceniem czy destrukcją nie tylko od obciążenia od strony gruntu, lecz także od strony hali. Należy przy tym uwzględnić tzw. trwałość eksploatacyjną całej podłogi oraz możliwe sposoby i koszty naprawy.
Konstrukcje i elementy konstrukcyjne powinny być projektowane, budowane i utrzymane w taki sposób, aby nadawały się do użytku w sposób ekonomiczny w okresie przewidzianym w projekcie. W szczególności konstrukcja – z odpowiednim stopniem niezawodności – nie powinna wykazywać uszkodzeń w stopniu nieproporcjonalnym do pierwotnej przyczyny w wyniku takich wydarzeń, jak powódź, obsunięcie terenu, pożar, wybuch, lub w rezultacie błędów ludzkich (wymaganie odporności konstrukcji).
Odpowiedni stopień niezawodności należy określić, biorąc pod uwagę możliwe konsekwencje jej utraty, jak również koszt, zakres wysiłków i czynności niezbędnych do ograniczenia ryzyka zniszczenia (PN-ISO 2394:2000 „Ogólne zasady niezawodności konstrukcji budowlanych”).
Zabiegi, które powinny być podjęte, aby osiągnąć odpowiedni stopień niezawodności, obejmują w tym zakresie także zastosowanie właściwej hydroizolacji.
Izolacja przeciwwodna czy przeciwwilgociowa?
Odpowiedź na pytanie, kiedy w warstwach podłogi konieczna jest izolacja przeciwwodna, a kiedy wystarczy tylko izolacja przeciwwilgociowa, zależy oczywiście od obciążenia wilgocią (poziom wody gruntowej), ale również od warstwy użytkowej.
Generalnie izolację przeciwwodną stosuje się w przypadku możliwości występowania wysokiego poziomu wody gruntowej, ale nie jest to jedyny przypadek.
Drugim jest konieczność wykonania posadzki żywicznej, a trzecim – składowanie na powierzchni posadzki materiałów wrażliwych na wilgoć. Osobną kwestią jest obecność termoizolacji czy konieczność zabezpieczenia podłogi i wód gruntowych przed agresywnymi cieczami mogącymi oddziaływać na posadzkę.
Poniżej rozpatrzono dwa przypadki podłogi: bez warstwy termoizolacji i z tego rodzaju warstwą.
Przeczytaj także:
- Naprawa lub wymiana posadzki przemysłowej. Praktyczne wskazówki
- Betonowe posadzki przemysłowe w halach. Jak wzmocnić wierzchnią warstwę posadzki betonowej? DST czy żywica eposydowa?
Hydroizolacja pod płytą betonową w podłodze bez termoizolacji. Rodzaje i parametry stosowanych materiałów hydroizolacyjnych
To najczęściej spotykany przypadek, co nie oznacza, że nie jest podatny na błędy. Konieczne jest tu wykonanie warstwy oddzielającej posadzkę betonową (monolityczną płytę) od warstw podbudowy. Warstwa ta pełni dwie funkcje: ww. izolacji przeciwwilgociowej oraz warstwy poślizgowej. Często stanowią ją jedną lub dwie warstwy folii o grubości 0,2 mm. Nasuwają się tu pytania: czy taka grubość jest wystarczająca oraz czy może to być tylko jedna warstwa czy niezbędne są dwie, a także czy możliwe jest zastosowanie innych materiałów?
W literaturze technicznej wartość 0,2 mm pojawiła się już dawno i przyjęło się, że jest to najczęściej stosowana grubość folii izolacyjnych. Należy jednak przedtem przeanalizować wymagania stawiane powłoce wodochronnej oraz oddziałujące na nią obciążenia. Folia o grubości 0,2 mm może stanowić jedynie warstwę poślizgową (ale niebędącą izolacją przeciwwilgociową), to i tylko wtedy, gdy podłoże pod nią jest równe.
Przy dużych obciążeniach i szczelinach dylatacyjnych wykonanych w górnej granicy dopuszczalnych odległości lepiej ułożyć dwie warstwy folii. Położenie jednej warstwy folii o grubości 0,2 mm to bardzo „wygodne”, choć nie do końca poprawne rozwiązanie.
Tego rodzaju bezkrytyczne „łączenie” warstwy rozdzielającej z funkcją hydroizolacyjną może skutkować uszkodzeniem folii podczas wykonywania betonowej płyty podłogi. Taka warstwa nie sprawdzi się jednak jako izolacja przeciwwilgociowa, ponieważ folia grubości 0,2 mm jest bardzo wrażliwa na uszkodzenia ze względu na niską wytrzymałość mechaniczną, nie wspominając o możliwości szczelnego łączenia zakładów.
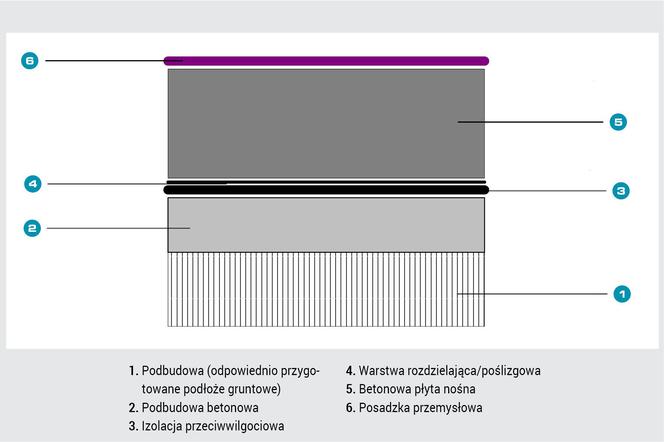
i
Hydroizolacja z folii z tworzyw sztucznych
Folie występują w kilku wariantach jako: jednorodne (niewzmacniane), zbrojone, wzmacniane, laminowane, a także wzmacniane i laminowane oraz zbrojone i laminowane.
Membrany te wykonywane są z różnych tworzyw, m.in.:
- ECB (ethylene copolymer bitumen),
- PIB (polyisobutylene),
- PVC-P (polyvinyl chloride),
- EVA (ethylene/polyetylene-vinyl acetate),
- FPO (flexible polyolefin),
- TPE (thermoplastic elastomer),
- PE (polyethylene),
- EPDM (ethylene propylene diene monomer).
W ramach tej samej grupy spotyka się folie bitumoodporne lub niebitumoodporne (np. PVC-P).
Podstawowym wymogiem dla folii jest możliwość szczelnego połączenia ze sobą arkuszy przez ich sklejenie czy zwulkanizowanie (przy zabezpieczeniu jedynie przed kapilarnym podciąganiem wilgoci teoretycznie wystarczy jedynie ułożenie arkuszy na zakład rzędu 20 cm, jednak to rozwiązanie nie ma nic wspólnego z wymogiem trwałości eksploatacyjnej i nie powinno być stosowane).
Istotne jest zatem określenie nie tylko grubości, lecz także innych parametrów (przede wszystkim wytrzymałościowych) zastosowanych folii, m.in.: szczelności, odporności na uderzenie, wytrzymałości na rozdzieranie (gwoździem), wytrzymałości złącza na ścinanie, maksymalnego naprężenia rozciągającego, maksymalnej siły rozciągającej oraz odporności na zginanie w niskiej temperaturze.
Przykładowe zalecenia można znaleźć w polskiej literaturze technicznej, np. dla folii stosowanych jako izolacja przeciwwodna:
- grubość ≥1 mm – folie PE i PP, a ≥1,5 mm – folie z PVC;
- brak przecieku przy ciśnieniu wody – min. 0,2 MPa przez 24 h;
- wytrzymałość na rozdzieranie (gwoździem) ≥100 N;
- wytrzymałość złącza na ścinanie – nie mniej niż 80–90% wytrzymałości wyrobu;
- dla wyrobów bez zbrojenia:
– maksymalne naprężenie rozciągające wzdłuż i w poprzek >15 N/mm2 dla wyrobów z tworzyw sztucznych oraz >6 N/mm2 dla tych na bazie kauczuku,
– wydłużenie przy zerwaniu w kierunku podłużnym i poprzecznym >250% dla wyrobów z tworzyw sztucznych oraz >300% dla tych na bazie kauczuku;
- dla wyrobów zbrojonych:
– maksymalna siła rozciągająca w kierunku podłużnym i poprzecznym >500 N/50 mm dla wyrobów z tworzyw sztucznych oraz >250 N/50 mm dla tych na bazie kauczuku,
– wydłużenie przy maksymalnej sile rozciągającej w kierunku podłużnym i poprzecznym >2% zarówno dla wyrobów z tworzyw sztucznych, jak i na bazie kauczuku.
Wprawdzie zalecenia te dotyczą zastosowania folii jako izolacji zagłębionych w gruncie części budynków i budowli, ale przyjęcie tych parametrów niejako przez analogię jest jak najbardziej uzasadnione. Zbieżne z powyższymi są wymagania norm niemieckich DIN 18533 („Abdichtung von erdberührten Bauteilen“) oraz DIN SPEC 20000-202 („Anwendung von Bauprodukten in Bauwerken – Teil 202: Anwendungsnorm für Abdichtungsbahnen nach Europäischen Produktnormen zur Verwendung als Abdichtung von erdberührten Bauteilen, von Innenräumen und von Behältern und Becken“).
Przykładowo, minimalna grubość folii stosowanych tylko do izolacji przeciwwilgociowej to:
- 1,2 mm – membrany z EVA, FPO czy PVC,
- 1,5 mm – membrany z ECB oraz PIB,
- 1,1 mm – EPDM.
W przypadku obciążenia wodą wymagane jest zastosowanie membran z:
- ECB o gr. 2 mm,
- PIB, PVC-P, EVA lub FPO o gr. 1,5 mm,
- EPDM o gr. 1,3 mm,
- EPDM o gr. 1,5 mm,
przy czym dodatkowo narzucone są inne, wspomniane powyżej parametry.
Wyjątek związany z grubością dotyczy izolacji wykonywanej na płycie fundamentowej (to chyba najbliższa analogia do analizowanego przypadku) przy obciążeniu wilgocią. Tu norma DIN SPEC 20000-202 dopuszcza stosowanie laminowanej folii z PE o grubości nie mniejszej niż 0,3 mm (grubość samej folii), jednak narzuca minimalne wartości parametrów, takich jak odporność na uderzenie i obciążenie statyczne czy maksymalne naprężenie rozciągające oraz maksymalna siła rozciągająca. Wymagane w tym przypadku parametry są oczywiście niższe niż dla folii o grubości 1 czy 1,5 mm, jednak taki zapis w praktyce wyklucza stosowanie przypadkowych folii o grubości 0,2 mm.
Należy pamiętać, że folie są bardzo wrażliwe na uszkodzenia mechaniczne (zwłaszcza na nierówności podłoża oraz uszkodzenia np. przy układaniu zbrojenia płyty żelbetowej), dlatego zawsze trzeba rozważyć zastosowanie warstwy ochronnej, np. z jastrychu cementowego czy dodatkowej wylewki betonowej.
Niezależnie od tego producent folii może narzucić konieczność stosowania dodatkowych warstw ochronnych, np. z geowłókniny.
Izolacja z rolowych materiałów bitumicznych
Do wykonania hydroizolacji można też użyć rolowych materiałów bitumicznych, takich jak papy polimerowo-bitumiczne lub samoprzylepne membrany, których parametry i cechy zależą głównie od rodzaju osnowy oraz sposobu i stopnia modyfikacji bitumu.
Właściwości poszczególnych rodzajów osnowy kształtują się następująco:
- welon szklany – stabilność wymiarów i masy;
- tkanina szklana – stabilność wymiarów i masy, wytrzymałość na rozerwanie, odporność na przebicie gwoździem oraz perforację;
- poliestrowa – wytrzymałość na rozerwanie, elastyczność (ciągliwość), odporność na przebicie gwoździem oraz perforację;
- mieszana z przewagą szklanej – wytrzymałość na rozerwanie, stabilność wymiarów, odporność na przebicie gwoździem oraz perforację;
- mieszana z przewagą poliestrowej – wytrzymałość na rozerwanie, elastyczność i (ciągliwość), stabilność wymiarów, odporność na przebicie gwoździem oraz perforację.
Samoprzylepne papy (membrany) mogą być także na osnowie z folii HDPE.
Masa asfaltowa, którą powleczona jest osnowa, najczęściej modyfikowana jest elastomerem SBS (styren-butadien-styren) lub plastomerem APP. Ten pierwszy nadaje papie stabilność formy, dobrą przyczepność do podłoża oraz znaczną elastyczność nawet w niskich temperaturach (do –40°C). Papy tego typu można łączyć z innymi rodzajami pap.
Plastomer APP (ataktyczne polipropyleny) z dodatkiem nasyconych elastomerów poliolefinowych oprócz stabilnej formy i dobrej przyczepności zapewnia odporność na działanie kwasów i soli nieorganicznych, ozonu oraz wysokiej temperatury (do 150°C). Taka papa staje się jednak dość sztywna w ujemnych temperaturach (–10°C).
Ze względu na działające obciążenie zaleca się stosować papy modyfikowane SBS-em, na osnowie poliestrowej lub mieszanej. Bezwzględnie wymagane jest sklejenie lub zgrzanie zakładów arkuszy. Pap na osnowie tekturowej, które gniją pod wpływem wilgoci, nie wolno stosować jako izolacji przeciwwilgociowej czy przeciwwodnej. Za to doskonale sprawdzają się jako warstwa ochronna w momencie wykonywania płyty betonowej posadzki. Zamiast tego typu papy można zastosować folię, tu grubość 0,2 mm nie stanowi przeszkody.
Odnośnie do parametrów samego materiału – dla pap termozgrzewalnych należy zwrócić uwagę m.in. na:
- gramaturę osnowy – dla papy poliestrowej powinna wynosić przynajmniej 180 g/m2, dla mieszanej przynajmniej 160 g/m2;
- zawartość składników rozpuszczalnych – nie powinna być mniejsza niż 2500 g/m2;
- maksymalną siłę rozciągającą wzdłuż i w poprzek – dla pap na osnowie: poliestrowej odpowiednio ≥800 N i ≥600 N, mieszanej: ≥600 N i ≥500 N;
- wydłużenie przy maksymalnej sile rozciągającej – dla pap na osnowie: poliestrowej ≥40%, mieszanej ≥2%;
- wytrzymałość złącza na ścinanie ≥150 N/50 mm lub zerwanie poza złączem;
- odporność na uderzenie – dla metody A niedopuszczalne przebicie powodujące przesiąkanie;
- wodoszczelność – 0,2 MPa;
- grubość – minimum 3 mm.
Izolacja podłogi pod termoizolacją
To inna sytuacja, w której warstwę rozdzielającą trzeba ułożyć na warstwie termoizolacji. Jej podstawową funkcją jest zabezpieczenie płyt termoizolacyjnych podczas wykonywania betonowej warstwy nośnej. W przypadku obciążenia tylko wodą, bez obecności agresywnych czynników (ewentualnie przy ich bardzo niewielkim stężeniu), można tu zastosować zwykłą folię z tworzywa sztucznego sklejaną lub zgrzewaną na zakładach (w przypadku braku obciążenia wilgocią od góry, układaną na zakład 20–30 cm).
W przypadku obciążenia posadzki agresywnymi mediami pod płytą betonową stosuje się membrany chemoodporne, sklejane lub zgrzewane na zakładach. Są one bezwzględnie wymagane w przypadku obecności agresywnych mediów działających destrukcyjnie na XPS (rozpuszczalniki: aceton, eter, octan etylu, nitro, benzen, ksylol, trójchloroetylen, czterochlorometan, terpentyna; węglowodory alifatyczne nasycone – cykloheksan, benzyna lakowa; paliwa silnikowe).
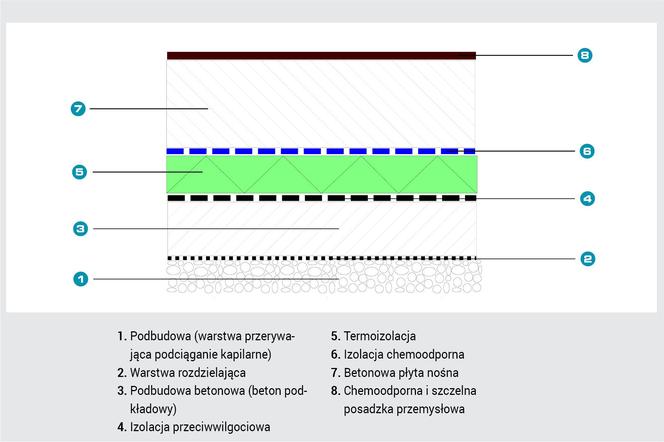
i
Do wykonywania tych chemoodpornych izolacji można stosować m.in. folie:
• z polichlorku winylu (PVC) – cechują się odpornością chemiczną na oddziaływanie kwasów organicznych, nieorganicznych i ługów (stężenia do 10–20%) oraz roztworów soli, a także olejów i tłuszczów; nie są odporne na oddziaływanie rozpuszczalników organicznych (m.in. benzenu, ksylenu);
• poliizobutylenowe – cechują się odpornością chemiczną na oddziaływanie kwasów organicznych i nieorganicznych o stężeniach do 20%, roztworów ługów o stężeniach do 30%, roztworów substancji utleniających i alkoholi (stężenia do 5–10%);
• polietylenowe z polietylenu wysokiej gęstości (HDPE) – cechują się odpornością chemiczną na oddziaływanie kwasów nieorganicznych o stężeniach do 20%, kwasów organicznych o stężeniach do 10%, ługów w 20–25% roztworach oraz na roztwory substancji utleniających (stężenie do 20–25%).
Odporna posadzka
Posadzki przemysłowe – warstwy użytkowe podłogi – muszą jednocześnie stanowić chemoodporne, ciągłe oraz szczelne dla wody i agresywnych mediów powłoki. Najczęściej są one wykonywane na bazie syntetycznych spoiw: epoksydowych, poliuretanowych, polimocznikowych i epoksydowo-poliuretanowych, dzięki którym gotowe posadzki uzyskują różne parametry i cechy, zależne również od grubości powłoki.
Posadzki epoksydowe stosuje się dla wysokich obciążeń mechanicznych i przy obecności agresywnych mediów. Żywice poliuretanowe w tego typu posadzkach wykorzystuje się tam, gdzie jest konieczność użycia materiału elastycznego, należy jednakże pamiętać, że odporność poliuretanów na oddziaływanie agresywnych substancji chemicznych jest mniejsza niż epoksydów.
Spotyka się także żywice poliuretanowo-epoksydowe charakteryzujące się większą odpornością mechaniczną i chemiczną niż posadzka poliuretanowa przy pewnej elastyczności, czego z kolei pozbawiona jest posadzka epoksydowa. Tego typu systemy cechują się zarówno elastycznością, jak i odpornością mechaniczną/chemiczną.
System posadzkowy zwykle składa się z gruntownika, warstwy mostkującej rysy i uszczelniającej oraz warstwy odpornej na ścieranie. Łączna grubość efektywnych warstw systemu wynosi zwykle od 2 do 5 mm. Taka kombinacja żywic wynika z wymagań stawianych systemowi: warstwa odporna na ścieranie przejmuje obciążenia mechaniczne, natomiast elastyczna zapewnia mostkowanie rys i szczelność. Dwuskładnikowe żywice poliuretanowe, w przeciwieństwie do epoksydowych, są jednak elastyczne, mają zdolność mostkowania rys podłoża oraz lepszą odporność na uderzenia, i to w niskich temperaturach.
Cechuje je także odporność na promieniowanie UV oraz starzenie. Ich parametry wytrzymałościowe są jednak niższe niż epoksydów, zwłaszcza dotyczy to odporności na ścieranie (wytrzymałość na rozciąganie rzędu 2,2–3,5 N/mm2, wydłużenie względne przy rozciąganiu do 160%). Charakteryzują się dobrą odpornością chemiczną, m.in. na paliwa (materiały pędne), smary, rozcieńczone kwasy i zasady, jak również na oleje, tłuszcze, aromatyczne węglowodory i estry. Wykazują mniejszą odporność na stężone zasady, zwłaszcza w podwyższonych temperaturach, oraz na ketony (BEB Arbeitsblatt „KH-0/S Stoffe“, 2002).