Spis treści
- Betonowa posadzka przemysłowa
- Warunki eksploatacji posadzki przemysłowej
- Podłoże/podbudowa
- Warstwa poślizgowa
- Płyta betonowa posadzki
- Szczeliny dylatacyjne w posadzkach betonowych
- Technologia DST
- Pielęgnacja posadzki betonowej
- Utwardzenie posadzki betonowej
- Podkład betonowy pod żywice epoksydowe
- Warunki wykonywania powłok epoksydowych
- Punkt rosy – wpływ na powłoki epoksydowane
W środowisku budowlanym ciągle istnieje potrzeba popularyzacji zagadnień związanych z posadzkami przemysłowymi. Długoletnie marginalizowanie tej tematyki, zarówno w procesie kształcenia kadry inżynierskiej, jak i w literaturze fachowej, przyczyniły się do powstania stereotypowego przekonania, że uszkodzenie posadzki to tak naprawdę nic groźnego, ponieważ nie powoduje bezpośredniego zagrożenia życia jej użytkowników. Utwierdzanie tego przekonania zaowocowało dość lekceważącym podejściem do zagadnienia projektowania, jak i wykonawstwa.
- Czytaj też: Posadzki przemysłowe w halach magazynowych - specyfikacja dla projektanta, wykonawcy i dostawcy regałów
Należy to zmienić, gdyż posadzki stanowią najintensywniej eksploatowane i najczęściej naprawiane elementy hali, ponieważ na nich koncentruje się całość obciążeń eksploatacyjnych danego obiektu. Ich awaria niejednokrotnie grozi wyłączeniem z użytkowania części lub nawet całości obiektu i stratami finansowymi. Komfort użytkowania każdego budynku halowego jest nieodłącznie związany z jakością posadzki przemysłowej. Jej wykonawstwo trudno przyporządkować do określonej specjalności budowlanej, zarówno z powodu skomplikowanych uwarunkowań projektowych, jak i realizacyjnych. Wymaga współdziałania wielu specjalistów zajmujących się m.in. gruntoznawstwem budowlanym, teorią projektowania, chemią budowlaną, technologią betonu oraz specjalistycznym wykonawstwem.
W artykule omówiono najistotniejsze aspekty związane z poszczególnymi elementami technologii betonowych posadzek przemysłowych, które nie są związane z podbudową, czyli tzw. pływających. Scharakteryzowano dwa najpopularniejsze sposoby wzmocnienia ich warstwy wierzchniej – wykończenie w technologii DST oraz przy wykorzystaniu powłok epoksydowych. Nadmierne ścieranie betonowych posadzek przemysłowych jest jednym z głównych problemów technicznych występujących w okresie ich eksploatacji, dlatego też o wyborze ostatecznej technologii jej wykonania decyduje kryterium ścieralności. W 80% przypadków stosowana jest technologia DST, w pozostałych 20% wykorzystuje się powłoki żywiczne (w przeważającej większości epoksydowe).
Betonowa posadzka przemysłowa
W literaturze technicznej przyjęto, że posadzka to element konstrukcyjny budowli, na który składają się wszystkie warstwy spoczywające na rodzimym podłożu gruntowym, uczestniczące w przenoszeniu na nie obciążeń. Ich układ jest następujący:
- rodzime podłoże gruntowe (współpracujące z posadzką),
- warstwa nośna posadzki, która w zależności od potrzeb składa się z:
– geosyntetyku (geosiatki, geotkaniny lub geowłókniny) o funkcjach głównie separacyjnych i wzmacniających,
– podbudowy z odpowiednio zagęszczonego, wzmocnionego lub chemicznie stabilizowanego gruntu nasypowego,
– podkładu z bardzo dobrze zagęszczonego sypkiego materiału gruboziarnistego (np. z grubego piasku, żwiru, pospółki, żużla, keramzytu czy tłucznia) z ewentualnym wzmocnieniem geosyntetykiem,
– podkładu z chudego betonu,
- warstwa poślizgowa i warstwa izolacji przeciwwilgociowej,
- betonowa warstwa konstrukcyjna w postaci płyty ze zbrojeniem rozproszonym lub ciągłym w układzie krzyżowym.W wymienionych powyżej warstwach pominięte zostały powłoki wykończeniowe, których głównym zadaniem jest podniesienie odporności powierzchniowej i walorów estetycznych posadzki.
Warunki eksploatacji posadzki przemysłowej
Gruntowna analiza warunków eksploatacji konkretnej posadzki to jeden z kluczowych etapów poprzedzających jej wykonanie. Zadanie to należy do projektanta obiektu. Niestety na etapie projektowania często można jedynie mniej lub bardziej trafnie przewidzieć, w jaki sposób rzeczywiście będzie wykorzystywana. Niedostosowanie założeń projektowych do warunków eksploatacyjnych to, oprócz błędów materiałowych i wykonawczych, jedna z głównych przyczyn powstawania uszkodzeń posadzki.
Na co zatem zwrócić uwagę na etapie poprzedzającym jej wykonanie? Przede wszystkim należy dokładnie przeanalizować potencjalne rodzaje obciążeń na nią oddziałujących:
- statyczne, np. punktowe od regałów, równomiernie rozłożone, blokowe, liniowe,
- dynamiczne, m.in. od wózków podnośnikowych, pojazdów transportowych, śmigłowców, samolotów, maszyn i urządzeń o wpływach dynamicznych,
- montażowe, np. od dźwigów używanych do montażu maszyn produkcyjnych,
- mechaniczne, pochodzące od zainstalowanych maszyn i urządzeń,
- chemiczne, m.in. od kwasów czy olejów,
- termiczne, np. równomierne bądź nierównomierne ochłodzenie i ogrzanie,
- wywołane skurczem betonu.
Podłoże/podbudowa
Na obszarach zurbanizowanych coraz częściej brakuje terenów o korzystnej budowie podłoża gruntowego, co zmusza inwestorów do wznoszenia obiektów na obszarach o gorszych warunkach posadowienia. Z tego powodu bardzo istotna jest rola prawidłowej oceny geotechnicznych warunków współpracy posadzki z podłożem. Najogólniej sformułowane wymagania stawiane podłożu gruntowemu to: odpowiednia nośność, uregulowane i stabilne warunki wodne oraz właściwe i równomierne zagęszczenie na całej powierzchni.
Zmiana któregoś z tych warunków w trakcie eksploatacji jest częstym powodem pojawienia się uszkodzeń posadzki. Parametrami charakteryzującymi w sposób ilościowy wytrzymałość warstwy nośnej i podłoża są moduły odkształcenia – pierwotny Ev1, i wtórny Ev2, oraz współczynnik podatności podłoża k wyrażony w N/mm3. Moduł Ev2 powinien odpowiadać wartości założonej w projekcie posadzki, ale nie może być niższy niż Ev2 = 80 N/mm2. Stosunek Ev2/Ev1 winien zaś spełniać warunek Ev1/Ev2 < 2,5.
Jeśli podbudowa nie jest odpowiednio wytrzymała, koniecznie należy ją poprawić lub przeprojektować konstrukcję posadzki przez takie zabiegi, jak zwiększenie jej grubości, zmianę klasy betonu, zwiększenie ilości zbrojenia rozproszonego i/lub użycie dodatkowego zbrojenia z siatek.
Podłoże pod posadzkę powinno być równe (dopuszczalne nierówności do 10 mm pod dwumetrową łatą), pozbawione miejscowych zaniżeń, a przede wszystkim przewyższeń, ostrych, wystających krawędzi. Lokalne zakotwienie płyty betonowej w podłożu to najczęstszy powód powstawania rys i spękań typu skurczowego. Podłoże gruntowe można przykryć warstwą betonu podkładowego klasy C8/10 lub C12/15, zwykle o grubości 100 mm, i dopiero na nim układać płytę posadzkową. Warstwa ta jest odporna na uszkodzenia, np. od kół betonomieszarek.
Warstwa poślizgowa
Swobodny przesuw płyty posadzki po odpowiednio przygotowanym podłożu umożliwia warstwa poślizgowa. Jej zadaniem jest zredukowanie wartości tarcia pod płytą posadzki, dlatego też należy ją wykonać z dwóch warstw folii polietylenowej o grubości nie mniejszej niż 0,2 mm. Współczynnik tarcia dla pojedynczej folii ułożonej na podłożu z chudego betonu wynosi 0,6−0,8. Zastosowanie dwóch warstw folii pozwala go zmniejszyć do wartości 0,3−0,5. Poszczególne warstwy folii należy ułożyć równo, bez fałd, z co najmniej 0,5-metrowymi zakładami.
Płyta betonowa posadzki
Grubość płyty posadzki jest zawsze określana na podstawie obliczeń statycznych i zależy od:
- nośności podłoża,
- rozstawu dylatacji konstrukcyjnych,
- wielkości obciążeń,
- typu zastosowanego zbrojenia,
- wymagań użytkowych posadzki.
Niezależnie od wyników obliczeń statycznych zaleca się, aby jej grubość nie była mniejsza niż 120 mm. Płyta posadzkowa musi mieć odpowiednią sztywność. Jej brak przyczynia się do paczenia krawędzi konstrukcyjnych, a to w konsekwencji prowadzi do powstawania zarysowań lub pęknięć płyty w ich pobliżu. Decydującym parametrem, z uwzględnieniem którego powinno się projektować beton do wykonania posadzki, jest skurcz.
Przyjmuje się, że jego całkowita wartość przy prawidłowo zaprojektowanym betonie używanym do wykonania posadzki nie przekracza 0,5 mm/m dla płyt zdylatowanych w sposób tradycyjny oraz nie więcej niż 0,4 mm/m dla płyt o specjalnych wymaganiach.
Wybór klasy betonu jest kompromisem między otrzymaniem betonu odpornego na ścieranie i zarazem o ograniczonym skurczu. Tylko zapewnienie jego odpowiednio niskiej wartości gwarantuje, że na posadzce z prawidłowo wykonanymi przerwami dylatacyjnymi nie pojawią się rysy i spękania typu skurczowego. Naprężenia spowodowane skurczem kompensowane są najczęściej przez dodanie do mieszanki betonowej odpowiednio efektywnych włókien stalowych.
Zazwyczaj wykonuje się posadzki z betonu klasy C20/25, C25/30 i C30/37, który jest w stanie zapewnić wymaganą wartość sił przyczepności włókien stalowych, pozwalających na pełne wykorzystanie ich efektywności i osiągnięcie przez fibrobeton odpowiednich właściwości mechanicznych i użytkowych. Mieszanka betonowa powinna być jednorodną masą, bez oznak sedymentacji.
Dodanie do niej włókien stalowych bardzo często wymusza zastosowanie większej ilości plastyfikatorów czy superplastyfikatorów, aby uzyskać właściwą konsystencję i urabialność. W ostatnim czasie do zbrojenia posadzek coraz częściej używa się odpowiednich włókien syntetycznych.
Szczeliny dylatacyjne w posadzkach betonowych
Szczeliny izolacyjne oddzielają posadzkę od innych elementów konstrukcji obiektu w celu umożliwienia ruchów dwóch sąsiednich elementów. Należy stosować je na stykach podłogi ze ścianami, słupami, fundamentami maszyn oraz budynku lub w innych miejscach mogących ograniczać ruchy podłogi zarówno w poziomie, jak i w pionie, np. przy piecach, osadnikach, kanałach instalacyjnych, schodach.
Powinny one całkowicie przecinać płytę podkładu. Jakiekolwiek połączenie posadzki z konstrukcją budynku generuje bowiem niepożądane naprężenia w posadzce. Szczeliny izolacyjne najczęściej wykonuje się poprzez obłożenie ścian, słupów, studzienek, doków czy naroży wchodzących w płytę posadzki pianką polietylenową. Ponadto miejsca te powinny być dodatkowo dozbrojone od mogących wystąpić naprężeń, np. za pomocą stalowych siatek i/lub prętów.
Mają za zadanie zlikwidować naprężenia oraz przypadkowe pęknięcia związane ze skurczem przy wysychaniu, zmianami termicznymi i wilgotnościowymi podłogi. W tym celu nacina się płytę betonową na głębokość ok. 1/3 jej grubości. Pod wykonanym nacięciem, gdzie struktura betonu jest osłabiona, następuje kontrolowane pęknięcie płyty betonowej i jej podział na pola dylatacyjne.
Szczeliny przeciwskurczowe umożliwiają ruch pól w poziomie, a dzięki zazębieniu pęknięcia pod nacięciem uniemożliwiają ruch w pionie. Jeśli projekt posadzki nie stanowi inaczej, to szczeliny dzielą posadzkę na pola prostokątne i kwadratowe o powierzchni nie mniejszej niż 36 m2, których długość boku nie powinna przekraczać 6 m.
Wykonywane są na styku betonów wylewanych w różnym czasie. Oddzielają płytę posadzki na całej grubości, uniemożliwiają ruch sąsiednich pól w pionie, lecz pozwalają na ich przesuwanie się w poziomie. W tym celu w szczelinach najczęściej stosuje się dyble albo zbrojenie łączące sąsiednie pola dylatacyjne, ewentualnie są one odpowiednio uformowane (zamki).
Technologia DST
Technologia DST (ang. Dry Shake Topping) polega na rozłożeniu i mechanicznym wtarciu w będący w fazie wiązania beton tzw. mineralnej posypki utwardzającej. Uzyskana w ten sposób wierzchnia warstwa płyty o grubości 2−3 mm ma przede wszystkim wysoką twardość i wytrzymałość mechaniczną, co czyni ją odporną na ścieranie. Niezależnie od przyjętej metody rozkładania betonu i rodzaju użytego utwardzacza utwardzenie w technice DST wykonuje się według następujących etapów:
- ręczne lub mechaniczne rozsypanie utwardzacza w określonej dawce na świeżą płytę betonową,
- wyrównanie i wygładzenie listwą ściągającą utwardzacza nasiąkniętego mleczkiem cementowym,
- wstępne zacieranie za pomocą dysku zakładanego na łopatki zacieraczki mechanicznej, wykonywane po częściowym stwardnieniu betonu, czyli w momencie, gdy można wejść na jego powierzchnię, pozostawiając ślad o głębokości 2−3 mm,
- mechaniczne zacieranie posadzki, wykonywane w określonych odstępach czasu, zależnych od panującej temperatury, przy użyciu zacieraczek mechanicznych zaopatrzonych w łopatki, których nachylenie zwiększa się w miarę utwardzania betonu. Klasyfikację suchych posypek utwardzających zamieszczono w tab. 1.
Odnosi się ona do ich składu i związanego z nim parametru ścieralności określanego metodą Böhmego. W ostatnich latach do określania ścieralności posadzki coraz częściej używana jest metoda BCA (ang. British Cement Association), wywodząca się z norm brytyjskich. Polega ona na pomiarze na powierzchni gotowej posadzki głębokości śladu powstałego po 2850 obrotach trzech stalowych, hartowanych kół przymocowanych do urządzenia badawczego, wirujących z prędkością 180 obr./min.
Przeprowadzenie pojedynczego badania zajmuje kilkanaście minut. Ponadto można je zrealizować w warunkach budowy, przy możliwie minimalnym uszkodzeniu powierzchni posadzki, a wyniki niejednokrotnie warunkują jej odbiór. Procedura badawcza symuluje długoterminowe obciążenia mechaniczne posadzki w sposób przyspieszony – wynik badania obrazuje zużycie posadzki po 25 latach eksploatacji.
Coraz większa liczba producentów posypek utwardzających deklaruje jedynie parametr ścieralności określony tą metodą, co nie ułatwia np. projektantowi doboru materiału odpowiedniego do warunków użytkowania. Pomocna w tym zakresie jest norma brytyjska BS 8204-2:2002, w której poszczególnym klasom odporności na ścieranie przyporządkowano warunki użytkowania i odpowiadające im limity testów ścieralności (tab. 2).
Pielęgnacja posadzki betonowej
Sposób pielęgnacji zależy od rodzaju warstwy wierzchniej posadzki. Jest ona szczególnie istotna w przypadku zastosowania technologii DST – zaleca się zabezpieczenie powierzchni posadzki bezpośrednio po jej wykonaniu przez nałożenie preparatu pielęgnacyjnego, tzw. folii w płynie, i/lub przykrycie folią. Akrylany znajdujące się w preparacie, nie w pełni chronią powierzchnię posadzki od wysychania, dlatego też najczęściej trzeba ją przykryć folią polietylenową.
W przypadku wykończenia posadzki pod nałożenie powłok żywicznych pielęgnację zazwyczaj ogranicza się do przykrycia folią. Z uwagi na osiąganie przez beton projektowanej wytrzymałości po 28 dniach zaleca się utrzymywanie nawilżenia płyty poprzez położenie na jej powierzchni 2−3-milimetrowej włókniny zabezpieczonej od góry folią. W rozwiązaniu tym włóknina absorbuje wodę i zatrzymuje ją nawet na kilka tygodni.
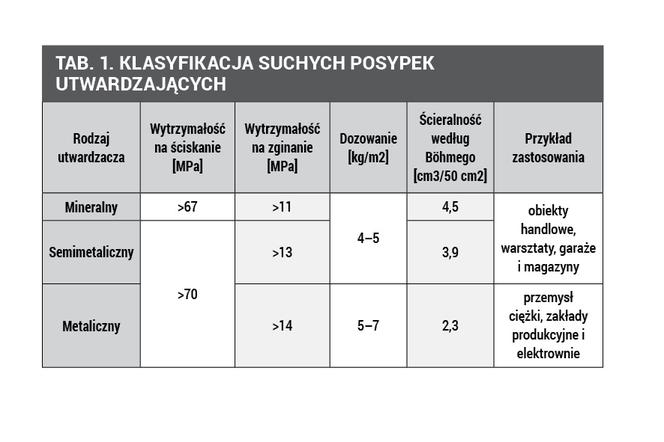
i

i
Utwardzenie posadzki betonowej
Żywice epoksydowe to ciekłe materiały polimerowe wykorzystywane w przemyśle od połowy XX wieku. W budownictwie sprawdzają się jako powłoki nakładane na powierzchnie betonowe, zwłaszcza te intensywnie eksploatowane. Dzięki niemal kilkudziesięcioletniej praktyce stosowania Eurokodów w świadomości inżynierskiej coraz mocniej zakorzeniło się podejście do projektowania uwzględniające trwałość konstrukcji.
Zapewnienie jej, zwłaszcza w przypadku posadzek przemysłowych, nie jest zadaniem łatwym i coraz częściej wiąże się z użyciem odpowiednich powłok. W ponad 95% przypadków powłoka posadzkowa jest materiałem kompozytowym składającym się z dwóch składników: ciekłego − spoiwa żywicznego, i stałego − wypełniacza w postaci piasku kwarcowego, mielonej żywicy stałej itp.
Kompozyt ten może dodatkowo zawierać: rozpuszczalniki, plastyfikatory, stabilizatory i barwniki. Posadzki z żywic epoksydowych układane są warstwami o grubości od kilkuset mikrometrów do kilku milimetrów. Niezwykle rzadko spotyka się posadzki jednowarstwowe.
Z uwagi na różne wymagania w zależności od typu posadzki żywicznej pomiędzy warstwą gruntującą a wierzchnią mogą być wykonywane różne warstwy pośrednie, pozwalające na spełnienie odpowiednich wymagań użytkowych, takich jak: antypoślizgowość, odprowadzanie ładunków elektrycznych, odporność na obciążenia mechaniczne, termiczne i inne, a także estetycznych, np. barwa, faktura, połysk, zmatowienie. Ww. warstwy scharakteryzowano w tab. 3.
Żywice epoksydowe używane do posadzek mogą być stosowane w formie dwuskładnikowej farby rozpuszczalnikowej lub dyspersji (impregnaty, posadzki cienkopowłokowe) albo w postaci bezrozpuszczalnikowej (posadzki grubopowłokowe i spoiwa do jastrychów).
Procedura powlekania podkładu betonowego żywicą składa się najczęściej z następujących czynności:
- zagruntowanie podłoża żywicą o niskiej lepkości (zazwyczaj dwuskładnikową) za pomocą wałka lub pędzla,
- posypanie zagruntowanej powierzchni piaskiem kwarcowym o uziarnieniu 0,1–0,4 lub 0,2−0,7 mm,
- wylanie i rozprowadzenie pacą zębatą powłoki wierzchniej,
- wyrównanie i odpowietrzenie wierzchniej warstwy wałkiem kolczastym.
Właściwie dobrana nawierzchnia epoksydowa:
- zwiększa wytrzymałość na ściskanie wierzchniej warstwy betonu,
- jest szczelna − zapobiega pyleniu, wchłanianiu brudu i chemikaliów,
- nie wymaga zabiegów konserwacyjnych,
- poprawia jakość warunków pracy i estetykę pomieszczenia,
- ma dużą odporność mechaniczną i chemiczną,
- nie ma żadnych łączeń (łatwa do utrzymania w czystości nawierzchnia bezspoinowa).
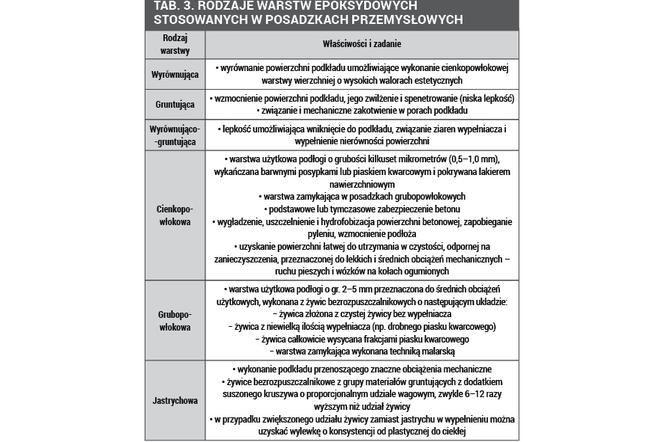
i
Podkład betonowy pod żywice epoksydowe
Podkład pod posadzki epoksydowe należy wykonać z betonu o klasie wytrzymałości na ściskanie co najmniej C20/25. Podłoże powinno być odpowiednio zwięzłe – dla uzyskania optymalnego zespolenia systemu powłokowego z podłożem odporność powierzchni na odrywanie musi wynosić co najmniej 1,5 MPa. Parametr ten można określić za pomocą aparatu pull-off. W metodzie tej nakleja się i w kontrolowany sposób odrywa stemple pomiarowe o dokładnie zdefiniowanej powierzchni.
Ponadto podłoże betonowe musi być lekko chropowate i mieć otwartą strukturę porów, a także czyste, pozbawione ubytków, zabrudzeń w postaci pyłu, kurzu, luźnych fragmentów oraz oczyszczone z mleczka cementowego i pozostałości preparatów chemicznych pogarszających przyczepność, takich jak: olej, smar, tłuszcz, nafta, środki antyadhezyjne. Jego odpowiednie przygotowanie ma na celu wielokrotne zwiększenie tzw. powierzchni czynnej podłoża, dzięki czemu poprawia się zdolność zakotwienia powłoki epoksydowej w podkładzie.
Najczęściej w tym celu wykonuje się: szlifowanie, śrutowanie lub frezowanie. Ponadto podłoże powinno być suche, wysezonowane przez co najmniej 28 dni, pozbawione wykwitów, rys i spękań. Powłoki epoksydowe są wodo- i paroszczelne, dlatego kluczowe znaczenie dla ich trwałości ma wysuszenie i zabezpieczenie podkładu betonowego przed wnikaniem wilgoci od spodu, podciąganiem kapilarnym (sprawna izolacja pozioma) oraz przygotowanie z odpowiednią tolerancją co do równości powierzchni, najczęściej mierzoną za pomocą dwumetrowej łaty kontrolnej, a w razie konieczności ukształtowanie z wymaganymi spadkami. Odchylenie powierzchni podkładu od płaszczyzny poziomej nie powinno przekraczać 5 mm na całej długości łaty dwumetrowej w każdym badanym miejscu i kierunku.
- Może zainteresuje Cię też: Plac Pięciu Rogów: miejska oaza, betonowa pustynia czy zwornik łączący różne przestrzenie i funkcje miasta?
Niestety, mimo że żywice są określane jako samopoziomujące, nie wygładzą nierównej powierzchni podłoża. Dodanie większej ilości produktu jedynie powoduje zwiększenie zużycia żywicy i tym samym kosztów wykonania posadzki. Nie ma również możliwości wykonania nawierzchni epoksydowej ze spadkiem na poziomym podłożu. Dopuszczalna wilgotność podłoża betonowego wynosi 4−5%. Jeżeli jest większa, należy zastosować specjalne preparaty gruntujące, mające za zadanie zabezpieczenie powłoki przed odspojeniem.
Niektóre bezrozpuszczalnikowe odmiany żywic utwardzają się nawet przy wilgotności 6−7%, zaś pewne dyspersje wodne można układać jako impregnat na beton w dowolnym czasie, nawet na świeżą mieszankę. Wilgotność określa się metodami niszczącymi, takimi jak suszarkowo-wagowa i karbidowa (CM), oraz nieniszczącymi, m.in. elektrycznymi i radiowymi. Wadą pierwszych jest duża pracochłonność i miejscowe zniszczenie podkładu związane z koniecznością pobrania próbek. Aby były one miarodajne, trzeba wykonać kilka pomiarów w różnych miejscach podkładu.
Należy zaznaczyć, że są one wrażliwe na obecność pyłu powstałego podczas nawiercania, który może zafałszowywać wyniki, ponieważ podczas tego procesu materiał nagrzewa się i odparowuje z niego wilgoć.
Metody nieniszczące, mimo że są mniej dokładne, stosuje się coraz powszechniej, bo umożliwiają szybkie, wyrywkowe i bezinwazyjne badanie. Dzięki temu pozwalają na podjęcie błyskawicznych decyzji odnośnie do rozpoczęcia, kontynuacji lub przerwania prac. Lekko wilgotne podłoże jest najczęściej przyczyną tzw. zmleczenia żywic już w kilkadziesiąt minut po ich ułożeniu. W takim przypadku żywicę należy usunąć w całości i aplikować od nowa.
Warunki wykonywania powłok epoksydowych
Powłoki epoksydowe powinno się wykonywać po zakończeniu wszystkich robót budowlanych, wykończeniowych i instalacyjnych, a więc w obiekcie szczelnie zamkniętym, zabezpieczonym przed wpływem czynników atmosferycznych. Miejsce, w którym będą realizowane, należy wydzielić i zabezpieczyć przed ogólnym dostępem, a także przed bezpośrednim wpływem robót zakłócających, takich jak: kucie, cięcie, szlifowanie, zagęszczanie gruntu, podsypki itp. Bardzo ważne jest również zapewnienie właściwego, tj. możliwie równomiernego, oświetlenia, zwłaszcza naroży i krawędzi posadzki, ponieważ w tych miejscach zwykle gromadzi się największa liczba pęcherzy.
Przed aplikacją materiałów podłoże trzeba dokładnie odpylić i odkurzyć. Aby wykonana powłoka nie była lepka, miękka i nie wykazywała przebarwień, koniecznie trzeba skontrolować terminy przydatności stosowanych produktów i ściśle przestrzegać zaleceń podanych w kartach technicznych. Żywice epoksydowe to złożone związki chemiczne wymagające zachowania należytych środków ostrożności. Pomieszczenia, w których będą wykorzystywane, powinny mieć sprawną wentylację.
Szkodliwe substancje zawarte w żywicach mogą wnikać do organizmu człowieka przez usta, skórę, oczy lub drogi oddechowe i być przyczyną zatruć, podrażnień dróg oddechowych, alergii, oparzeń, zawrotów głowy i nudności. Pracownicy powinni mieć odpowiednią odzież, obuwie, maski, okulary i rękawice ochronne, a także nie używać w pobliżu stanowisk pracy otwartego ognia. Podczas chodzenia po świeżej żywicy trzeba stosować specjalne nakładki (kolce) na buty, a w czasie szlifowania podłoża betonowego lub stwardniałej żywicy − maski z filtrem przeciwpyłowym. Składniki żywic są toksyczne, a także szkodliwe dla organizmów wodnych i mogą powodować długo utrzymujące się zmiany w środowisku wodnym.
Dlatego też należy je przewozić i przechowywać w szczelnie zamkniętych, oryginalnych opakowaniach w celu uniknięcia zanieczyszczenia środków transportowych i urządzeń magazynowych. Produkty oznaczone symbolem zagrożeń chemicznych i niebezpiecznych dla środowiska muszą być pakowane zgodnie z wymaganiami przewozu towarów niebezpiecznych. Resztki i pozostałości żywic należy dostarczyć na składowisko odpadów niebezpiecznych.
Temperatura i wilgotność powietrza w czasie wykonywania powłoki epoksydowej
Na końcową jakość powłoki epoksydowej ma wpływ temperatura powietrza, podłoża oraz materiału. Temperatura podkładu w trakcie wykonywania oraz utwardzania się powłoki powinna być wyższa niż 15°C. Żywice bezpośrednio przed aplikacją powinny mieć ją równą lub porównywalną do tej, jaką ma podkład. Temperatury zbliżone do 8°C wydatnie opóźniają czas twardnienia, zwiększają lepkość i utrudniają właściwe rozprowadzenie materiału, co w rezultacie może prowadzić do jego podwyższonego zużycia, a także problemów z odpowietrzeniem. Te osiągające 25−30°C przyspieszają twardnienie i skracają czas obróbki, ale przez to utrudniają uzyskanie powłoki o optymalnej jakości. Nieraz po prostu może zabraknąć czasu na odpowietrzenie rozlanej żywicy za pomocą wałka.
Przygotowywanie żywic do stosowania i ich aplikowanie powinny odbywać się w miejscu suchym, zabezpieczonym przed wpływami atmosferycznymi, o temperaturze powietrza od 15 do 25°C oraz wilgotności względnej nieprzekraczającej 70%. Okres letni nie sprzyja realizacji powłok epoksydowych, ponieważ często występujące opady deszczu oraz wysoka temperatura powietrza powodują intensywne parowanie wody, w rezultacie czego utrzymują wilgotność powietrza na poziomie 80−95%. W trakcie prac bardzo niebezpieczne są przeciągi, przyczyniające się do tzw. naskórkowywania powłoki, czyli powstawania nierówności na jej powierzchni. Po zakończeniu tego etapu prac, należy zapewnić podane w karcie technicznej produktu warunki pielęgnacji i utwardzania się położonej warstwy. Czas, po którym uzyska ona optymalne parametry umożliwiające jej eksploatację, powinien być zgodny z podanym przez producenta.
Pomieszczenie trzeba dobrze wentylować zarówno podczas jej wykonywania, jak i w czasie utwardzania. Jeżeli warunki temperaturo-wilgotnościowe są niekorzystne, wymagane jest stosowanie grzejników. Gdy podłoże betonowe jest suche, a wilgotność powietrza zbyt duża na powierzchni żywicy po kilku godzinach od jej położenia tworzy się biały nalot. Zazwyczaj usuwa się go przez szlifowanie i ponowne nałożenie żywicy w tym samym kolorze. Podczas wykonywania kolejnych powłok żywicznych wilgoć może przyczynić się do ich rozwarstwienia lub pojawienia się pęcherzy. Z tego też powodu należy unikać rozpoczynania prac w czasie, gdy migracja wilgoci jeszcze trwa, np. w godzinach porannych i przedpołudniowych w okresie letnim.
Punkt rosy – wpływ na powłoki epoksydowane
Punkt rosy to temperatura powierzchni, przy której następuje kondensacja wilgoci z powietrza (jest ściśle związany z jego wilgotnością względną). Jeżeli wynosi ona 100%, to jest on równy z istniejącą temperaturą, co oznacza, że przy danej jej wartości powietrze jest maksymalnie nasycone wilgocią. Temperatura punktu rosy to ta, przy której para wodna zawarta w powietrzu staje się nasycona (przy zastanym składzie i ciśnieniu powietrza), a poniżej niej przesycona i skrapla się lub resublimuje.
Punkt rosy jest jednym z krytycznych aspektów związanych z wykonywaniem powłok epoksydowych. Może być on przyczyną złej przyczepności, zmniejszenia trwałości czy pogorszenia właściwości położonej powłoki. Para wodna, szczególnie w okresie zimowym, w zetknięciu z chłodną powierzchnią podkładu betonowego, ulega wykropleniu i powoduje powierzchniowe chwilowe zawilgocenie podłoża. Kondensat pary wodnej obniża przyczepność. W celu zachowania praktycznego marginesu bezpieczeństwa oraz aby zapobiec tworzeniu się wilgoci kondensacyjnej, temperatura podłoża musi być o co najmniej 3°C wyższa od punktu rosy.
Zwykle w miarę postępu robót warunki cieplno-wilgotnościowe zmieniają się, dlatego też konieczne jest stałe monitorowanie parametrów wpływających na punkt rosy, czyli temperatury i wilgotności względnej powietrza. Temperaturę punktu rosy można obliczyć za pomocą tabeli punktów rosy lub coraz powszechniej używanych elektronicznych termohigrometrów.