Spis treści
Korozja jest niestety zmorą większości obiektów przemysłowych, w których ważną rolę odgrywają różnego rodzaju konstrukcje i instalacje stalowe. Zwłaszcza, jeśli są one narażone na działanie niekorzystnych warunków środowiskowych, chemicznych lub mechanicznych (przede wszystkim wilgotne powietrze, ale również kwasy, sole, zanieczyszczone powietrze czy naprężenia mechaniczne). Stal, jako materiał szczególnie podatny na korozję elektrochemiczną, wymaga stosowania odpowiednich środków ochronnych, żeby zapewnić długowieczność i niezawodność konstrukcji.
Polecany artykuł:
Jak zapobiegać korozji w warunkach przemysłowych?
Walka z korozją może i powinna być prowadzona różnymi metodami. Już na etapie projektowania jest możliwe dobranie odpowiednich materiałów dla danych konstrukcji (np. stali kwasoodpornej, żaroodpornej czy z odpowiednimi dodatkami stopowymi, ale również stali wykończonej różnymi sposobami odróbki cieplnej lub cieplno-chemicznej). Istotna może być także sama konstrukcja danej instalacji przemysłowej czy też zastosowane elementy łączeniowe lub mocujące.
Z kolei już w trakcie eksploatacji konstrukcji stalowych niezbędne jest prowadzenie odpowiednich działań, których celem jest oczyszczanie powierzchni narażonych na korozję, naprawa ewentualnych uszkodzeń, a także kontrola środowiska i eliminowanie z niego niekorzystnych czynników.
Ważnym elementem ochrony antykorozyjnej są również wszelkiego rodzaju powłoki ochronne (np. powłoki malarskie czy galwaniczne), których głównym celem jest odizolowanie powierzchni stalowej od otoczenia. Niezbędne jest naturalnie uzupełnianie na bieżąco wszelkich ubytków w takich powłokach. Do tej grupy środków ochronnych zaliczamy również inhibitory korozji, które – po wprowadzeniu do korodującego środowiska – spowalniają reakcje korozyjne na powierzchni metalu.
I choć powyższe metody są coraz skuteczniejsze, nie zawsze zapewniają pełną ochronę przed korozją. Dlatego też często równolegle stosuje się tzw. ochronę katodową, która ma dodatkowo zabezpieczać stalowe powierzchnie przed korozją elektrochemiczną.
Na czym polega ochrona katodowa powierzchni stalowych
Ochrona katodowa przed korozją należy do grupy elektrochemicznych metod ochronnych. Polega ona na stworzeniu takich warunków, w których chroniony przed korozją element staje się katodą w układzie elektrochemicznym, dzięki czemu procesy korozyjne zostają zminimalizowane lub całkowicie zatrzymane.
W systemie ochrony katodowej stalowy element jest połączony z anodą – metalem, który jest bardziej podatny na korozję. Zwykle stosuje się materiały takie jak cynk, magnez czy aluminium, które łatwiej ulegają procesowi utleniania. Dzięki temu stalowy obiekt, pełniący rolę katody, nie koroduje, ponieważ proces korozji nie zachodzi na jego powierzchni.
Ochrona katodowa znajduje szerokie zastosowanie przede wszystkim w zabezpieczeniu konstrukcji stalowych, które są narażone na długotrwały kontakt z wodą lub są zainstalowane pod ziemią. Najczęściej stosuje się je w przypadku podziemnych i podwodnych rurociągów czy zbiorników stalowych, ale z powodzeniem ochronę tę można zastosować również np. do elementów konstrukcyjnych hal przemysłowych czy innych obiektów (np. mostów). W przypadkach tych drugich ochrona katodowa pozwala na znaczną poprawę trwałości i niezawodności infrastruktury, eliminując lub minimalizując procesy korozji, które mogłyby prowadzić do poważnych uszkodzeń.
W praktyce stosuje się dwa główne typy systemów ochrony katodowej: systemy galwaniczne i systemy z wymuszonym prądem.
Polecany artykuł:
Ochrona katodowa galwaniczna (systemy z anodą galwaniczną)
W tej metodzie ochrony przed korozją wykorzystuje się anodę z metali aktywnych, takich jak cynk, magnez czy aluminium. Nie wymaga ona stosowania zewnętrznego źródła prądu, dzięki czemu jest to rozwiązanie efektywniejsze, a jednocześnie proste w instalacji.
Zasada działania systemu galwanicznego opiera się na tym, że anoda, będąca metalem bardziej podatnym na korozję, przekazuje prąd ochronny do chronionego obiektu. Prąd ten sprawia, że powierzchnia stalowa (lub inna metalowa) staje się katodą, na której nie zachodzi proces utleniania, czyli korozji. W tym układzie anoda, zwana protektorem, z czasem ulega zużyciu, zabezpieczając jednocześnie chroniony obiekt przed szkodliwym działaniem środowiska korozyjnego.
W praktyce anoda może przybierać formę powłok na metalu (np. cynkowa powłoka stalowa) lub specjalnie rozmieszczonych płyt wykonanych z metali aktywnych. Podstawowym celem tego systemu jest przesunięcie potencjału elektrochemicznego chronionego metalu w stronę wartości elektroujemnych, co zapobiega jego korozji.
Główną zaletą ochrony katodowej galwanicznej jest jej prostota – system jest łatwy do zainstalowania i nie wymaga skomplikowanej konserwacji. Z tego względu jest szczególnie polecany do mniejszych instalacji, w miejscach, gdzie nie ma potrzeby stałej kontroli przepływu prądu ani dostępu do zewnętrznego źródła zasilania. Tego typu ochrona jest stosowana m.in. w przypadku rurociągów, zbiorników wodnych czy elementów podwodnych, gdzie dostęp do zasilania jest utrudniony.
Ochrona katodowa galwaniczna ma jednak również pewne ograniczenia. Anody ulegają zużyciu, co wiąże się z koniecznością ich wymiany po pewnym czasie. Ponadto jej efektywność jest ograniczona do mniejszych instalacji i obiektów, w których częsta wymiana anod nie jest dużym problemem.
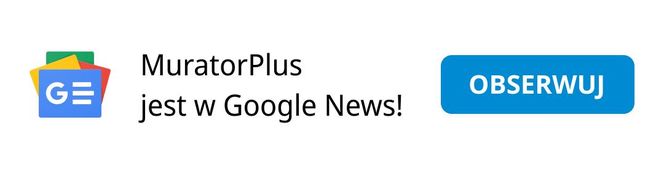
Ochrona katodowa elektrolityczna (systemy z zewnętrznym źródłem zasilania)
W tym systemie ochrony przed korozją prąd jest dostarczany do chronionych elementów stalowych za pomocą specjalistycznego prostownika. W efekcie służy do elektrochemicznego neutralizowania procesów korozji, utrzymując stałą ochronę katodową na powierzchniach metalowych.
Zasada działania tej metody ochrony antykorozyjnej sprowadza się do tego, że chroniony element staje się katodą w elektrochemicznym ogniwie, które jest zasilane prądem z zewnętrznego źródła. Zewnętrzne zasilanie, często realizowane przez nowoczesne stacje mikroprocesorowe, pozwala na precyzyjne monitorowanie stopnia ochrony i optymalizowanie pracy systemu.
Główne zalety systemów z wymuszonym prądem to ich wysoka efektywność, zwłaszcza w przypadku dużych instalacji i w trudnych warunkach środowiskowych (instalacje podziemne i podwodne). Umożliwiają ponadto precyzyjne kontrolowanie poziomu ochrony, co pozwala na skuteczną i długotrwałą ochronę przed korozją. Jednak ich stosowanie wiąże się z koniecznością zapewnienia stałego źródła zasilania i regularnego monitorowania systemu, co zwiększa koszty instalacji i eksploatacji w porównaniu z systemami ochrony galwanicznej.
Choć systemy ochrony katodowej z wymuszonym prądem wymagają większych inwestycji początkowych i regularnego nadzoru, stanowią bardzo efektywną metodę ochrony dużych instalacji przed korozją, oferując precyzyjne i długotrwałe zabezpieczenie przed uszkodzeniami.
Podsumowanie
Ochrona katodowa jest obecnie jednym z najbardziej efektywnych i powszechnie stosowanych sposobów zapobiegania korozji w konstrukcjach stalowych, szczególnie w środowiskach agresywnych chemicznie. Dzięki znaczącemu wydłużeniu żywotności stalowych elementów przedsiębiorstwo może ograniczyć koszty związane z ich konserwacją, a także zwiększyć bezpieczeństwo eksploatacyjne danej instalacji.
- Zobacz również: Certyfikowane obiekty przemysłowe w Polsce