Spis treści
- Systemy IT w logistyce magazynowej - jakie rozwiązanie sprawdza się najlepiej?
- Hala produkcyjna to skomplikowany obszar logistyczny
- Analiza logistyczna w zakładzie produkcyjnym - jak się za to zabrać?
- Grupy materiałów i ich składowanie - istotny punkt analizy. Dlaczego?
- Analiza przepływu materiałów w hali produkcyjnej - co trzeba określić?
- Funkcjonalności systemu IT w hali produkcyjnej - co zyskujemy?
- Oznakowanie miejsc składowania - na co zwrócić uwagę?
Jaką technologię składowania wybrać? Jaki typ środków transportu wewnętrznego będzie optymalny ze względu na pracochłonność? Jak zaprojektować układ funkcjonalno-przestrzenny magazynu, aby zminimalizować czasy przejazdów? A może zastosować elementy automatyki magazynowej, aby zmechanizować niektóre procesy magazynowe? Pytania te wpłynęły na rozwój rynku dostawców różnych usług i produktów, podsycając dodatkowo chęć optymalizacji w tym zaniedbanym do niedawna obszarze logistyki, jakim był magazyn.
Systemy IT w logistyce magazynowej - jakie rozwiązanie sprawdza się najlepiej?
Po roku 2000, wraz z rosnącą popularnością wykorzystywania systemów IT w różnych obszarach biznesowych, takich jak ERP czy CRM, dostrzeżono również logistykę magazynową. Polskie firmy coraz śmielej odkrywały zalety stosowania systemów WMS lub TMS, usprawniających wszystkie procesy, które zachodzą w magazynach, popularnych już od wielu lat w krajach, które miały szansę rozwijać się w wolnorynkowych warunkach.
Zobacz także: Innowacje w logistyce magazynowej - przykłady, trendy!
Obecnie trudno sobie wyobrazić powstanie magazynu bez przeprowadzania niezbędnych analiz logistycznych, obejmujących również funkcjonalności systemu WMS. Według obserwacji autora rocznie wykonuje się od 20 do 40 wdrożeń systemów WMS krajowych i zagranicznych dostawców, nie wspominając o istotnej liczbie wdrożeń korporacyjnych (roll-out) w polskich oddziałach zagranicznych firm. Ponadto coraz więcej przedsiębiorstw zwraca uwagę również na logistykę na terenie zakładu, wokół budynków odwiedzanych nawet przez kilkaset samochodów dziennie. Dlatego też popularniejsze stają się systemy YMS (z ang. Yard Management System), wspomagające zarządzanie ruchem środków transportu oraz pieszych, oferowane jako osobny element lub część systemu WMS.
Obecnie wydaje się, że logistyka w wielu firmach została już dobrze przeanalizowana, a procesy magazynowe w istotny sposób usprawniono. Firmy dysponujące dużymi magazynami wiedzą, że aby utrzymać pozycję rynkową, muszą usprawniać procesy magazynowe.
Co jednak w sytuacji, gdy firma zajmuje się produkcją i magazyn wyrobów gotowych jest jednym z wielu elementów, przez które przepływają materiały czy wyroby gotowe? W takich przypadkach prawdziwym wyzwaniem jest nie tyle znalezienie dogodnej lokalizacji dla wyrobu gotowego, ile przede wszystkim optymalne dostarczenie odpowiedniej ilości materiału w żądanym czasie do właściwej linii produkcyjnej. Następnie zaś bez zbędnego oczekiwania należy wyrób gotowy odstawić do najwłaściwszej lokalizacji, co przy całej złożoności zakładu przemysłowego jest już łatwą decyzją dla systemu IT.
Hala produkcyjna to skomplikowany obszar logistyczny
Zakład przemysłowy w wielu firmach stanowi jeden z najbardziej skomplikowanych obszarów logistycznych. Mamy tu bowiem do czynienia m.in. z takimi procesami jak:
- przyjęcia do obszarów magazynowych bardzo różnorodnych pod względem struktury dokumentów zakupu oraz postaci fizycznej surowców czy półfabrykatów;
- realizacja przepływów według kolejek FIFO, LIFO, FEFO i innych bardzo specyficznych dla różnych firm produkcyjnych metod;
- składowanie właściwych surowców i półfabrykatów blisko punktów ich dostarczania, m.in. linii produkcyjnych czy też obszarów pakowania;
- obsługa materiałów pomiędzy różnymi procesami produkcyjnymi, w tym ich śledzenie oraz tymczasowe składowanie;
- tworzenie zestawów dla klientów końcowych w obszarze produkcyjnym, a także ich właściwe procesowanie w kontekście systemów IT;
- obsługa dużej ilości różnorodnych (ze względu na postać fizyczną) materiałów, wracających do miejsc składowania ze stanowisk produkcyjnych;
- organizacja pracy zapewniająca sprawny przepływ informacji i materiałów na styku obszarów funkcjonalno-przestrzennych oraz odpowiedzialności magazyn – produkcja;
- właściwe oznakowanie i identyfikacja przeróżnych (ze względu na postać fizyczną) materiałów, półfabrykatów oraz wyrobów gotowych.
Z doświadczeń autora niniejszego artykułu wynika, że wiele firm produkcyjnych do tej pory nie dokonało dogłębnej analizy przepływu materiałów i informacji. Co więcej, zdarza się, że obszar produkcyjny bywa pomijany jako istotny element kosztów logistycznych wytworzenia wyrobu gotowego i sytuuje się go w ramach szeroko pojętej dystrybucji towaru.
Zobacz także: Przemysł 4.0 - magazyny i logistyka w przedsiębiorstwie produkcyjnym
Konieczność utrzymywania przewagi konkurencyjnej wymusza jednak na firmach produkcyjnych wykonanie analizy następujących aspektów m.in. w zakresie:
- zapewnienia sprawnej wymiany informacji na styku magazyn – produkcja;
- gwarancji pełnego śledzenia materiałów przy uwzględnieniu zwrotów z produkcji;
- minimalizacji liczby przejazdów pomiędzy różnymi obszarami magazynowymi i produkcyjnymi;
- ukształtowania obszarów funkcjonalno-przestrzennych przy uwzględnieniu składowania różnych materiałów, które są wymagane do zasilania różnorodnie rozmieszczonych linii produkcyjnych;
- częstotliwości i ilości dostarczania materiału do linii produkcyjnych;
- odpowiedniego czasu i sposobu dokonywania konsumpcji surowców na linii produkcyjnej.
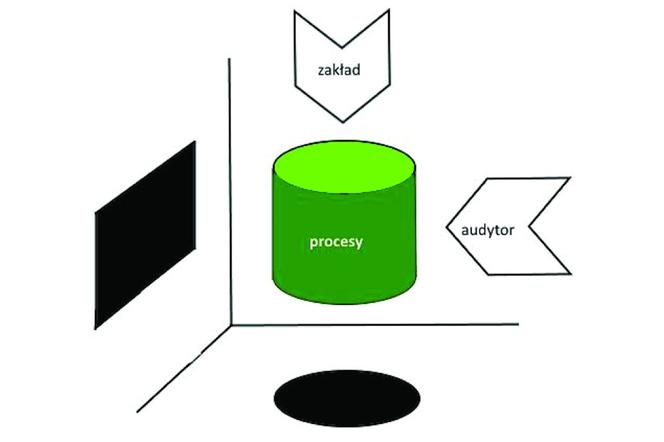
i
Analiza logistyczna w zakładzie produkcyjnym - jak się za to zabrać?
Analizę logistyczną powinno się zlecić firmie z odpowiednim doświadczeniem zdobytym przy realizacji projektów doradczych w obszarach produkcyjnych. Jeśli nawet firma produkcyjna dysponuje zespołem odpowiedzialnym m.in. za udoskonalanie przebiegających w niej procesów biznesowych, po pewnym czasie nie jest on w stanie dostrzec niektórych strat czy błędów w ich funkcjonowaniu, ponieważ nie ma odniesienia do ich organizacji w przedsiębiorstwach o podobnym profilu biznesowym.
Zobacz także: Audyt logistyczny. Co to jest audyt logistyczny? Na czym polega audyt? Po co przeprowadza się audyt?
Osoba z zewnątrz często już w pierwszym dniu wizyty w zakładzie potrafi zauważyć pewne ograniczenia lub błędy, do jakich pracownicy byli od wielu lat przyzwyczajeni. Często audytorzy są zatrudniani dopiero wówczas, gdy trzeba rozbudować halę produkcyjną lub magazynową. Audytor zewnętrzny, obserwując procesy w zakładzie przemysłowym, może dojść do zupełnie innych wniosków niż wewnętrzny zespół, który od dawna pracuje z danymi rozwiązaniami.
Na rys. zwizualizowano podejście do procesów zachodzących w zakładzie z punktu widzenia pracowników i audytorów. Pierwsi z nich szukają wszelkich niedoskonałości (kątów), ale w pewnym momencie już ich nie dostrzegają, a wynik wykonanych obserwacji, zaprezentowany w postaci koła, pozbawiony jest jakichkolwiek kątów (wad). Natomiast audytor zewnętrzny ma duże szanse, aby te same procesy prześwietlić z nieco innej strony, w wyniku czego rzucają one cień w kształcie prostokąta, co sugeruje konieczność optymalizacji (likwidacji kątów).
Poniżej przedstawiono przykładowy zakres prac analitycznych realizowany dla zakładu produkcyjnego, który planuje uruchomienie nowego obszaru magazynowego.
Etap A – ANALIZA WYMAGAŃ
- A1. Rozpoczęcie projektu i wizyta w zakładzie.
- A2. Zbieranie danych.
- A3. Weryfikacja i analiza danych.
Etap B – OPRACOWANIE KONCEPCJI WSTĘPNYCH
- B1. Określenie wstępnych koncepcji logistycznych w kilku (2–3) wariantach projektowych dla reorganizacji przepływu towarów w zakładzie.
- B2. Określenie wstępnych koncepcji logistycznych w kilku (2–3) wariantach projektowych.
- B3. Wyznaczenie potrzebnej przestrzeni/powierzchni dla różnych wymaganych obszarów funkcjonalnych.
- B4. Ogólny, wstępny dobór urządzeń i wyposażenia dla każdego wariantu koncepcji.
- B5. Opracowanie wstępnych rysunków ukształtowania w nowych obszarach magazynowych (początkowa wizja, rysunki w rzucie z góry).
- B6. Przybliżenie poziomu nakładów inwestycyjnych.
- B7. Analiza SWAT dla każdej z koncepcji (plusy, minusy, charakterystyka pracy itp.) dla obszarów magazynowych i przepływów w zakładzie.
- B8. Spotkanie warsztatowe – prezentacja koncepcji wstępnych i wybór jednej z nich do szczegółowego opracowania.
Etap C – OPRACOWANIE KONCEPCJI KOŃCOWEJ
- C1. Dokładny dobór urządzeń (regały, wózki, przenośniki, owijarki, stoły itd.) wraz z podaniem nazw producentów i typów. Analiza kosztów zakupu, utrzymania i warunków serwisowych.
- C2. Projekt organizacji pracy (ogólne wytyczne, podział zadań, uwagi i sugestie).
- C3. Projekt procesów (opis sposobów realizacji procesów: przyjmowania towarów, transportu, komisjonowania itd.).
- C4. Projekt przestrzenny (lokalizacja stref, ich wielkości itp.).
- C5. Opis systemu składowania (rodzaj i miejsce składowanych towarów), liczba półek i miejsc paletowych, powierzchnie, przestrzenie itp.
- C6. Opis systemu transportu (typ urządzeń, wymagane parametry itp.).
- C7. Weryfikacja pracochłonności procesów (obliczenia w oparciu o dane statystyczne pochodzące z metody MTM).
- C8. Obliczenia nakładów i kosztów rocznych dla wybranego wariantu.
- C9. Projekt reorganizacji przepływów pomiędzy różnymi obszarami składowania w zakładzie (propozycje dotyczące lokalizacji i systemów składowania, urządzeń transportowych oraz dróg transportu wewnętrznego).
- C10. Wykonanie dokumentacji rysunkowej (AutoCAD) i opisowej.
- C11. Spotkanie z klientem celem przedstawienia wyników, wykonania ostatnich poprawek i uaktualnień w projekcie.
- C12. Uaktualnienia i rekalkulacje. Weryfikacje danych wyjściowych.
- C13. Opracowanie końcowej dokumentacji rysunkowej i opisowej.
Grupy materiałów i ich składowanie - istotny punkt analizy. Dlaczego?
Jednym z najważniejszych punktów w całej analizie logistycznej jest identyfikacja grup materiałowych pod kątem:
- cech fizycznych,
- częstotliwości oraz wielkości dostaw do linii produkcyjnych,
- lokalizacji linii produkcyjnych zasilanych daną grupą materiałową,
- sposobu składowania oraz wykorzystywanych środków transportu wewnętrznego.
Kolejną czynnością powinno być odwzorowanie lokalizacji przechowywania grup materiałowych oraz przebieg ich przepływu na planie zakładu produkcyjnego z wykorzystaniem w tym celu np. narzędzi graficznych z funkcją obsługi warstw, z których każda reprezentuje składowanie oraz przepływy danej grupy materiałowej.
Wbrew pozorom wykonanie tego ćwiczenia nie jest takie łatwe, gdyż wymaga od audytora zbadania wszystkich „zakamarków” w zakładzie produkcyjnym. Już na wczesnym etapie prac można przeprowadzić krótką prezentację wyników takiej analizy. Autor niniejszego artykułu kilkakrotnie był świadkiem, jak zarząd z niedowierzaniem patrzył na wizualizację tras, które przebiegały przez cały teren zakładu tylko dlatego, że ktoś przypadkowo zdecydował o lokalizacji danej grupy materiałowej.
Raz podjęte decyzje zostały przyjęte jako obowiązująca reguła i przez dłuższy czas nikt nie zastanawiał się, czy przypadkiem danej grupy materiałowej nie składować np. bliżej linii produkcyjnych.

i
Analiza przepływu materiałów w hali produkcyjnej - co trzeba określić?
Analiza przepływu materiałów i ich optymalizacja wymaga dużego nakładu prac analitycznych i na ostateczne ich wyniki należy poczekać nawet kilka miesięcy, jednak w trakcie realizacji zadania firma konsultingowa powinna dzielić się częściowymi wnioskami. Logistyka hal produkcyjnych dotyka m.in. bardzo popularnej ostatnio kwestii optymalizacji i śledzenia dostaw na linię produkcyjną.
Należy bowiem zwrócić uwagę na duży stopień skomplikowania tego procesu, w którym trzeba określić:
- maksymalną wielkość pojedynczej dostawy na linię produkcyjną,
- sposób dostawy,
- moment, w którym następuje decyzja dotycząca konieczności zasilenia linii produkcyjnej,
- maksymalną pojemność bufora przy linii produkcyjnej,
- maksymalną pojemność materiału na linii produkcyjnej przed jego przetworzeniem,
- sposób przekazania informacji o konieczności zasilenia linii produkcyjnej,
- moment konsumpcji materiału na linii produkcyjnej,
- sposób powiadomienia o konsumpcji materiału na linii produkcyjnej.
Jak wynika z ww. elementów, proces dostawy materiału na linię produkcyjną jest jednym z najbardziej skomplikowanych procesów logistycznych w zakładzie produkcyjnym. Systemy IT zazwyczaj mają możliwość wspierania dostaw materiałów, ale autor niniejszego artykułu niezwykle rzadko spotykał się z pełną automatyzacją przepływu informacji w tym obszarze.
Krytycznym elementem jest moment podjęcia decyzji o konieczności zasilenia linii produkcyjnej. W zdecydowanej większości przypadków następuje on wówczas, gdy pracownik linii produkcyjnej sam zauważa, że niedługo zabraknie mu materiału. Są jednak firmy, które testują rozwiązania umożliwiające automatyzację przepływu informacji.
W lokalizacjach buforowych instaluje się systemy, monitorujące zmniejszającą się ilość materiału i w momencie przekroczenia określonej granicy same wysyłają zadanie do magazynu celem uzupełnienia materiału w buforze produkcyjnym. Dzięki temu pracownik na linii produkcyjnej czy inna osoba odpowiedzialna za ten fragment procesu nie musi sygnalizować, że zachodzi taka konieczność. Ten, wydawałoby się, mało istotny element jest zdaniem autora jednym z najważniejszych procesów logistycznych w zakładzie produkcyjnym.
Funkcjonalności systemu IT w hali produkcyjnej - co zyskujemy?
Dobrze zaprojektowany system IT umożliwia w dużym stopniu automatyzację przepływu materiałów i informacji na styku magazyn – produkcja. Do jego najważniejszych funkcjonalności należą:
- praca na zadaniach z przeplataniem (inne nazwy: task interleaving, directed work, multicykle),
- możliwość zmapowania buforów przy liniach produkcyjnych oraz linii produkcyjnych wraz z ich pojemnościami,
- raportowanie ręczne lub automatyczne konsumpcji materiałów na linii produkcyjnej,
- możliwość automatycznego generowania zadań dostaw materiałów w małych partiach, zależnych od stanu zapełnienia buforów przy liniach produkcyjnych w odpowiednim czasie,
- sprawna obsługa procesu zwrotów materiałów w różnym stanie jakościowym z linii produkcyjnych,
- możliwość integracji z urządzeniami umożliwiającymi monitorowanie konsumpcji materiałów,
- obsługa zleceń produkcyjnych.
Poza procesem dostaw materiałów do linii produkcyjnych trzeba także uwzględnić sprawną obsługę przyjęć wyrobów gotowych z linii produkcyjnych. Do najważniejszych wymaganych funkcjonalności należą:
- sprawna obsługa BOM (z ang. Bill Of Material), umożliwiająca rozliczenie materiałów na podstawie wyprodukowanej liczby wyrobów gotowych,
- integracja z systemami do etykietowania,
- przyjmowanie na stan wyrobów gotowych na podstawie zleceń produkcyjnych,
- możliwość przyjmowania wyrobów gotowych w pełnych i niepełnych ilościach ładunkowych,
- automatyczne generowanie zadań przesunięć po rejestracji ładunku z wyrobem gotowym.
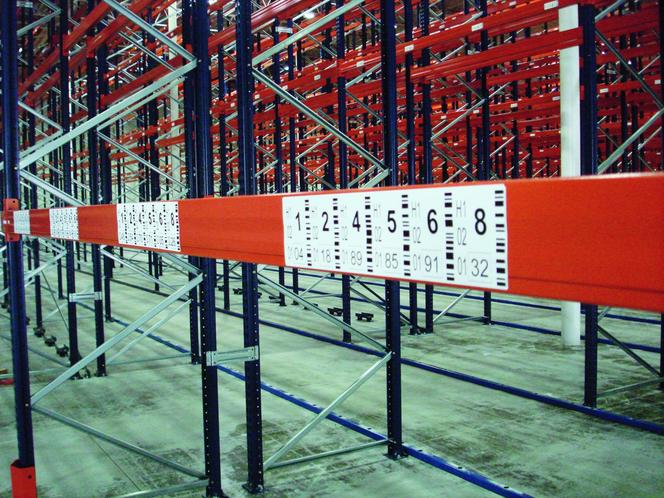
i
Oznakowanie miejsc składowania - na co zwrócić uwagę?
Logistyka zakładu przemysłowego to nie tylko przepływy i miejsca składowania, lecz także konieczność prawidłowego oznakowania tych miejsc oraz indeksów w taki sposób, aby systemy IT sprawnie wspierały przepływ materiałów. W obszarach magazynowych często mamy do czynienia z bardzo odmiennym pod względem fizycznym towarem, który może być składowany w różny sposób. Jeśli jest układany na posadzce, można zastosować tablice podwieszane, w przypadku regałów paletowych wykorzystuje się etykiety przyklejane na belkach magazynowych.
Należy pamiętać o tym, aby zapewnić etykietom:
- możliwie wysoki kontrast i dokładność wydruku,
- odpowiedni kąt przy podwieszaniu,
- wielkość dopasowaną do typu skanerów,
- trwałość (najlepiej wykorzystywać etykiety z tworzyw sztucznych zamiast z papieru).
Co więcej, można również zastosować dodatkowe oznaczenia, które zwiększają szybkość i pewność identyfikacji. W tym celu używa się:
- strzałek lub innych symboli na etykietach lokalizacyjnych w celu wyróżnienia np. poziomu składowania,
- różnych kolorów dla oznaczenia poziomu składowania,
- tablic informacyjnych z numerem rzędu lub korytarza roboczego montowanych na czole regałów magazynowych,
- dodatkowych malowanych oznaczeń na posadzce magazynowej.
Oznakowanie lokalizacji magazynowych można również zastosować na posadzce, ale należy pamiętać, że ich czytelność niezwykle rzadko udaje się utrzymać w dobrym stanie. Elementem logistyki w zakładzie przemysłowym są również prawidłowo oznakowane drogi transportu wewnętrznego oraz ciągi pieszych.
Często można spotkać się z sytuacją, gdzie elementy linii produkcyjnej znajdują się w skrajni drogi, powodując potencjalne niebezpieczeństwo ruchu. Gdy przeszkoda bardzo długo stoi w jednym miejscu, z czasem przestaje przeszkadzać wieloletnim pracownikom. Problem może pojawić się wraz z zatrudnieniem nowych, którzy będą musieli nauczyć się omijać przeszkody, stwarzając wówczas duże niebezpieczeństwo.
Zobacz także: Nowy park logistyczny w Toruniu będzie mieć 46 600 m2 powierzchni. Rusza budowa
Czytaj też:
- Automatyzacja procesów logistycznych. Przykłady automatyzacji, opis urządzeń
- Transport wewnętrzny. Inteligentny transport wewnętrzny w magazynach