Spis treści
System detekcji gazów powinien być zaprojektowany i wykonany tak, by mógł możliwie szybko rozpoznać i dokładnie wychwycić zagrożenie, a następnie ostrzec pracowników oraz powiadomić o niebezpieczeństwie obsługę hali, a także dać sygnał do uruchomienia innych systemów w celu eliminacji ryzyka. W związku z tym ważne jest właściwe rozmieszczenie czujników systemu detekcji, aby możliwie jak najdokładniej zlokalizować zagrożenie.
Nowoczesne systemy detekcji w obiektach przemysłowych składają się z detektorów (kilkudziesięciu) podłączonych do central sterujących, których pracę można podglądać w systemie sterowania budynkiem (BMS). Alarmy także pojawiają się w centralnym systemie sterowania, dzięki czemu dokładnie wiadomo, gdzie wystąpiło zagrożenie.
Rodzaje detektorów
Na rynku dostępny jest szeroki wachlarz urządzeń i czujników pomiarowych, które można podzielić ze względu na różne kryteria.
Ze względu na funkcje wyróżniamy czujniki:
- jednofunkcyjne – do pomiaru stężenia gazu niebezpiecznego, np. ziemnego;
- dwufunkcyjne – do pomiaru stężenia dwóch rodzajów gazów, np. ziemnego i tlenku węgla;
- wielofunkcyjne – do pomiaru stężenia gazu, temperatury, wilgotności itp.
Ze względu na sposób działania występuje podział na detektory:
- katalityczne – odpowiadają za detekcję i pomiar stężenia gazów niebezpiecznych; nie są wrażliwe na obecność innych gazów, dają możliwość ustawiania czułych (dokładnych) progów alarmowych, są stabilne w zmiennych warunkach atmosferycznych, a ich trwałość to 6–8 lat w warunkach bez zakłóceń innymi gazami. Dzięki konstrukcji składającej się z dwóch elementów (sensor i element reaktywny) mają bardzo dobre zdolności pomiarowe, są stosowane do pomiaru gazów wybuchowych;
- półprzewodnikowe – to najstarsza technologia, choć czasami nadal wykorzystywana. Służą do wykrywania i pomiaru stężenia gazów wybuchowych i toksycznych; sprawdzają się w miejscach, gdzie mierzony gaz nie występuje na stałe, a pojawia się tylko w wyniku usterki. Najlepiej funkcjonują przy pomiarach gazów jednorodnych, ich wadą jest czułość na zmianę temperatury otoczenia, są bardzo trwałe – mogą być używane nawet przez 8–10 lat. Ich zaletą jest niska cena. Do wad można zaliczyć głównie generowanie fałszywych alarmów;
- elektrochemiczne – mierzą stężenie gazów toksycznych; są dokładne i praktycznie nie reagują na inne gazy zakłócające, ich trwałość to 2–5 lat. Należą do grupy czujników selektywnych;
- infra-red (czujniki optyczne) – służą do pomiaru stężenia gazu, przy przekroczeniu jego dopuszczalnego stężenia następuje alarmowa sygnalizacja optyczna. Do ich zadziałania nie jest potrzebne zajście reakcji chemicznych ani obecność tlenu, są wysoce odporne na warunki atmosferyczne. Stosowane są w przepompowniach ścieków czy studzienkach. Należą do grupy czujników selektywnych;
- MPS (Molecular Property Spectrometr) – w odróżnieniu od pozostałych są to czujniki mierzące stężenie nie tylko jednego gazu. Informują o dolnej granicy wybuchowości (TrueLEL) różnych gazów lub mieszaniny gazów. Dodatkowo detektory klasyfikują gaz do odpowiedniej kategorii, co jest użyteczną informacją w przypadku ewentualnego zagrożenia.
Detektory gazów mogą pracować w sposób liniowy lub nieliniowy. Działanie liniowe oznacza, że sygnał sensora jest wprost proporcjonalny do poziomu stężenia mierzonego gazu. W przypadku urządzeń nieliniowych nie występuje ta zależność. Skutkuje to występowaniem fałszywych alarmów.
Granice wybuchowości gazów palnych
Główne kategorie zagrożeń gazami to:
- Ex – zagrożenie wybuchem gazów palnych i wybuchowych;
- Ox (tlen) – zagrożenie niedotlenieniem z powodu obniżonego stężenia tlenu lub zagrożenie zwiększoną palnością czy wybuchem wskutek podwyższonego stężenia tlenu;
- Tox – zagrożenie zatrucia gazami toksycznymi.
Dolna granica wybuchowości DGW lub LEL (lower explosive limit) określa, przy jakim stężeniu gazu palnego [% obj.] lub [g/m3] w palnej mieszance gaz-powietrze może nastąpić zapłon (atmosfera wybuchowa).
DGW wszystkich znanych gazów i par palnych zawierają się w zakresie od ok. 0,5 do 15% objętości, np. DGW mieszanki wodór-powietrze to 4% objętości – a więc gaz o stężeniu 2% objętości wodoru (który jest gazem wybuchowym) w powietrzu nie ulegnie zapłonowi. Jest to niezwykle istotna informacja dotycząca bezpieczeństwa – jeżeli gaz palny nie zapala się poniżej stężenia DGW, możliwe jest zastosowanie ochrony przeciwwybuchowej przez ciągłe monitorowanie stężenia tego gazu oraz zadbanie o to, by wartość połowy DGW (=50% DGW) nigdy nie została przekroczona.
Warto podkreślić, że najbardziej niebezpieczne są gazy palne o niskich dolnych granicach wybuchowości. W przypadku par palnych to temperatura oraz ciśnienie pary danej cieczy są decydującymi parametrami – im niższa temperatura, tym są bardziej niebezpieczne.
Oprócz dolnej granicy wybuchowości w nomenklaturze technicznej stosowana jest także górna granica wybuchowości GGW lub UEL (upper explosive limit), oznaczająca takie stężenie gazu, powyżej którego nie powstanie atmosfera wybuchowa, czyli nie dojdzie do zapłonu i palenia się czynnika w całej mieszaninie.
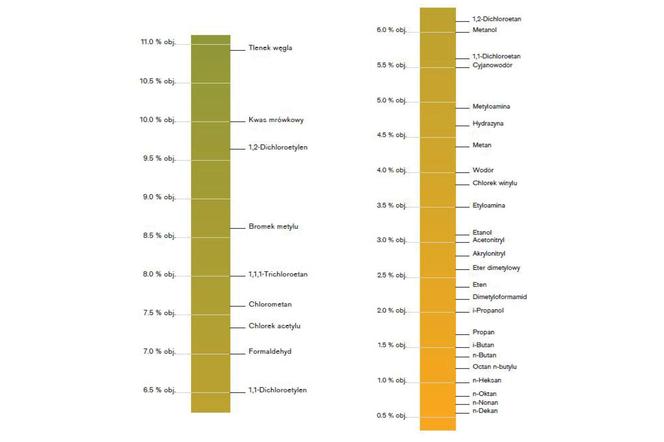
i
Wymagania i przepisy
Ogólne wymogi stawiane systemom detekcji gazów ujęte są w przepisach pożarowych oraz BHP. Urządzenia w tych instalacjach traktowane są jako:
- „zabezpieczające przed powstaniem wybuchu i ograniczające jego skutki” (Rozporządzenie Ministra Spraw Wewnętrznych i Administracji z dnia 7 czerwca 2010 r. w sprawie ochrony przeciwpożarowej budynków, innych obiektów budowlanych i terenów; DzU nr 109, poz.719);
- „zapewniające sygnalizację o zagrożeniach” (Obwieszczenie Ministra Gospodarki, Pracy i Polityki Społecznej z dnia 28 sierpnia 2003 r. w sprawie ogłoszenia jednolitego tekstu rozporządzenia Ministra Pracy i Polityki Socjalnej w sprawie ogólnych przepisów bezpieczeństwa i higieny pracy; DzU 2003 nr 169, poz. 1650, z późn. zm.).
Projekt systemu detekcji gazów wybuchowych musi zostać uzgodniony przez rzeczoznawcę ds. przeciwpożarowych. Jednak nie każdy system detekcji będzie podlegał przepisom pożarowym – niektóre instalacje służą wykrywaniu gazów toksycznych dla człowieka. Informują wtedy o przekroczeniu stężenia niebezpiecznego dla zdrowia i życia ludzkiego (m.in. tlenek węgla CO). Jeśli jednak w pomieszczeniu lub obiekcie może wystąpić przekroczenie dolnej granicy wybuchowości danego gazu, to należy instalację traktować jako rodzaj zabezpieczenia przeciwpożarowego. Kwalifikacja instalacji leży w gestii projektanta branżowego i wymaga znajomości specyfiki miejsca oraz branży.
Ważnym zagadnieniem jest określenie, czy system detekcji powinien działać podczas pożaru. To jednak wymaganie, które trudno spełnić ze względu na charakter przedmiotowej instalacji. W trakcie pożaru wydziela się szereg różnych gazów w postaci dymu, który zakłóca pracę detektorów. Ponadto zwykle same sensory nie są odporne na dym i ogień, podobnie jak pozostałe elementy instalacji, m.in. centrale czy przewody.
Obiekty przemysłowe w zależności od branży podlegają szeregowi przepisów odnośnie do wymagań stawianych systemowi detekcji. Oddzielne wymagania są dla produkcji wyrobów z gumy, inne dla przetwórstwa papieru, jeszcze inne dla tworzyw sztucznych, urządzeń energetycznych czy przy pracy w zakładach górniczych. Odrębnie traktowane są także wszystkie instalacje i obiekty związane z gazem ziemnym i płynnym.
Oprócz wymogów stawianych samemu systemowi istnieją również warunki, które muszą spełnić osoby wykonujące instalację. Zgodnie z Ustawą z dnia 10 kwietnia 1997 r. „Prawo energetyczne” (DzU nr 54, poz. 348, ze zm.) istnieje kilka grup uprawnień koniecznych do pracy w energetyce. Do montażu instalacji detekcji gazów potrzebne są uprawnienia:
• do pracy przy urządzeniach elektrycznych – I grupa;
• do pracy przy urządzeniach z paliwami gazowymi – III grupa;
• do pracy przy urządzeniach przeciwwybuchowych – grupa EX.
Przepisy regulują także kwestię przeglądów konserwacyjnych systemów detekcji gazów, które zgodnie z Rozporządzeniem Ministra Spraw Wewnętrznych i Administracji z 7 czerwca 2010 r. w sprawie ochrony przeciwpożarowej budynków, innych obiektów budowlanych i terenów (DzU 2010 nr 109 poz. 719) powinny być wykonywane przynajmniej raz w roku. Kwestia przeglądów poszczególnych urządzeń i czujników podana jest przez producenta w karcie urządzenia lub dokumentacji techniczno-ruchowej.
Przeczytaj również:
- Ochrona przeciwpożarowa - wymagania, zabezpieczenia, rozwiązania technologiczne
- Oddymianie garaży - co mówią przepisy? Jak projektować systemy oddymiania garaży?
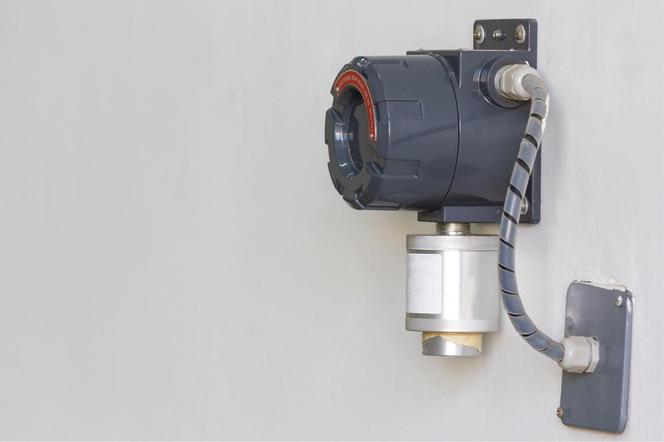
i
Wybór lokalizacji detektora
Odpowiednie umiejscowienie detektorów jest kluczowe dla właściwego działania całego systemu. W zależności od rodzaju gazu lokalizacja czujnika będzie inna:
- gaz lżejszy od powietrza (np. metan, wodór) – w bliskiej odległości, powyżej potencjalnego punktu wycieku;
- gaz o gęstości zbliżonej do powietrza (np. tlen) – na wysokości punktu wycieku, z uwzględnieniem kierunku ruchu powietrza;
- gazy toksyczne – na wysokości dróg oddechowych dorosłego człowieka;
- gaz cięższy od powietrza (np. dwutlenek węgla) – poniżej miejsca wycieku, blisko podłogi ze szczególnym uwzględnieniem potencjalnych martwych punktów.
Przy lokalizowaniu czujników niezwykle istotna jest bardzo dobra znajomość właściwości mierzonych gazów. Niektóre z nich mają specyficzne cechy, które należy uwzględnić – np. amoniak stosowany w różnego rodzaju urządzeniach chłodniczych ma tendencję do obłokowego przemieszczania się, w związku z czym detektory powinny być wyposażone dodatkowo w specjalne okapy.
Nowoczesne systemy mają zazwyczaj cztery progi alarmowe. Oznacza to, że w pierwszej kolejności pojawia się sygnał ostrzegawczy, następnie podejmowane są działania zapobiegawcze (np. odcięcie instalacji przez zamknięcie zaworu, uruchomienie wentylacji mechanicznej), kolejny krok to poinformowanie obsługi obiektu, a jeżeli to konieczne, zatrzymanie procesów technologicznych. Wstrzymanie produkcji to krok ostateczny ze względu na generowane koszty i brak ciągłości pracy.
Warto pamiętać, że oprócz pomiarów w poszczególnych strefach/pomieszczeniach istotne są także miejsca nietypowe, jak np. wnętrza rurociągów. Dlatego też system detekcji gazów musi być ściśle dostosowany do specyfiki produkcji i nie powinno być to typowe i schematyczne rozwiązanie.
Wskazówki praktyczne
Istotną rolę w systemie detekcji pełni właściwy dobór sensorów, tak by zminimalizować ryzyko wzbudzania fałszywych alarmów, jednocześnie gwarantując możliwie nieduże zużycie energii elektrycznej. Prawidłowo dobrane czujniki powinny szybko i skutecznie wykrywać ulatniający się gaz, nawet w otoczeniu innych gazów zakłócających.
Jedną z najważniejszych kwestii jest dokładne określenie rodzajów gazów występujących w obiekcie i dobranie do nich odpowiednich detektorów. Znajomość właściwości gazów pozwala na rozmieszczenie czujników w taki sposób, aby system jak najszybciej rozpoznał ewentualne zagrożenie.
Przy lokalizacji detektorów nie należy kierować się zasięgiem czujnika, ponieważ gazy nie rozprzestrzeniają się równomiernie w pomieszczeniu. Miejsce gromadzenia się wyciekającego gazu zależy od jego parametrów i charakterystyki (np. gęstości w odniesieniu do powietrza). Aby czujnik się uaktywnił, gaz musi się bezpośrednio do niego dostać. Niezwykle istotne jest, by detektory wykrywały gazy o stężeniu poniżej DGW.
Warto także zaznajomić się ze specyfiką danego zakładu i występujących w nim instalacji pod kątem słabych (usterkowych) punktów. Szczególną uwagę należy zwrócić na połączenia rurociągów, które są potencjalnym miejscem wycieku.
Kolejnym istotnym działaniem jest odpowiednia kalibracja czujników – tak, aby faktycznie wykrywały niebezpieczne stężenia gazów.
Bardzo ważnym aspektem jest też zapewnienie regularnej konserwacji instalacji technologicznych, jak i samego systemu detekcji. Utrzymanie urządzeń w wysokiej sprawności gwarantuje bezpieczeństwo i szybkie wykrywanie zagrożeń.