W hali o konstrukcji stalowej jej obudowa, tzn. ściany zewnętrzne czy dach, jest wykonywana w technologii ciężkiej lub lekkiej. Pierwsza z nich, realizowana za pomocą żelbetowych płyt prefabrykowanych stosowanych w konstrukcji dachu oraz ścian murowanych z bloczków silikatowych, gazobetonowych lub prefabrykowanych płyt gazobetonowych, jest obecnie praktycznie całkowicie wyparta przez obudowę lekką. W przypadku tej technologii najczęściej wykorzystuje się płyty warstwowe o konstrukcji: płaska lub profilowana blacha stalowa/rdzeń termoizolacyjny/płaska lub profilowana blacha stalowa. Przy czym jako jej wypełnienie na ogół stosowany jest styropian, sztywna pianka poliuretanowa (PUR) lub wełna mineralna.
Do zalet płyt warstwowych można zaliczyć ich dobre właściwości termoizolacyjne, małą wagę oraz wielkoformatowość, która znacznie ułatwia i skraca ich montaż. Jednak z punktu widzenia akustyki, wyroby te nie są efektywnym rozwiązaniem. Należy pamiętać, że w przypadku przegród jednorodnych lub warstwowych ich dźwiękoszczelność zależy głównie od masy powierzchniowej, zaś w znacznie mniejszym stopniu od konstrukcji (parametrów warstw).
W akustyce obowiązuje tzw. prawo masy, które mówi, że podwojenie masy przegrody powoduje zwiększenie jej izolacyjności akustycznej o 6 dB. Oznacza to również, że zmniejszenie masy znacznie obniża dźwiękoizolacyjność. W przegrodach warstwowych konstrukcja tylko trochę łagodzi tę zależność. Ponadto stosowanie cienkich blach, na ogół w zakresie 0,4–1,2 mm, a przede wszystkim sprężystość warstwy termoizolacyjnej, powoduje gwałtowne obniżenie dźwiękoszczelności dla wybranych częstotliwości.
Na rysunku przedstawiono typowe częstotliwościowe charakterystyki płyt warstwowych z wypełnieniem PUR o standardowej konstrukcji i grubościach. Takie panele cechuje mała izolacyjność akustyczna w zakresie niskich częstotliwości (kilkanaście dB), wyraźny jej spadek dla średnich oraz wysoki poziom dla dużych (około 50 dB). Ze względu na niską dźwiękoszczelność w zakresie małych i średnich częstotliwości wskaźniki jednoliczbowe przyjmują niewielkie wartości, np. Rw osiąga 25–28 dB. Ten sam dla przegrody żelbetowej o grubości 150 mm wynosi 54 dB. Co więcej, w przemyśle najczęściej występuje hałas o dużym natężeniu w zakresie małych częstotliwości. Oznacza to, że panele warstwowe nie sprawdzą się w roli przegrody, której celem jest ograniczenie hałasu na stanowisku pracy lub jego emisji w obrębie hali przemysłowej. Wartości R wyrażone za pomocą wskaźników oceny izolacyjności akustycznej właściwej typowych przegród budowlanych stosowanych w halach przemysłowych podano w tabeli.
Panele warstwowe z rdzeniem wykonanym ze styropianu mają praktycznie takie same właściwości dźwiękoizolacyjne, jak tych z wypełnieniem ze sztywnych pianek poliuretanowych. Nieco większą izolacyjnością akustyczną charakteryzują się płyty warstwowe z rdzeniem z wełny mineralnej. Mają one o ok. 10 dB większą dźwiękoszczelność dla małych i średnich częstotliwości oraz zbliżoną w zakresie dużych. Ponadto znaczne obniżenie izolacyjności akustycznej dotyczy wyższych częstotliwości i jest mniej drastyczne niż w panelach ze sztywnym wypełnieniem termoizolacyjnym.
Porównując wskaźniki tych produktów w tabeli można zauważyć, że te z rdzeniem z wełny mają o 9 dB większą izolacyjność, niż wyroby ze sztywnym wypełnieniem (PUR lub styropian). Należy także podkreślić, że masa panelu z wełną mineralną jest dwa razy większa niż płyty z pianką PUR, co potwierdza poprawność stosowania prawa masy przy ocenie izolacyjności akustycznej przegród warstwowych. Przy czym według niego panel z rdzeniem z wełny powinien mieć izolacyjność o 6 dB większą, natomiast przyrost o kolejne 3 dB wynika ze zmiany sztywności wypełnienia termoizolacyjnego oraz lepszych właściwości dźwiękochłonnych wełny w odniesieniu do pianek PUR lub styropianu.
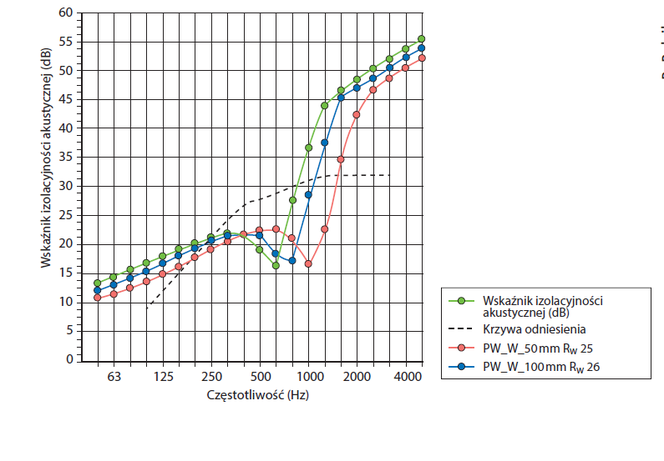
i
W przemyśle ciężkim hałas w halach może przyjmować wartości znacznie większe od 85 dB(A) , a nawet powyżej 100 dB(A). Co więcej, wiele maszyn stosowanych w takim sektorze emituje dźwięki przede wszystkim w zakresie małych częstotliwości. W związku z tym jedynym rozwiązaniem jest wykonanie przegrody ciężkiej, np. murowanej z masywnych pustaków, żelbetowej wylewanej lub prefabrykowanej, gdyż tylko ona umożliwi uzyskanie dużej izolacyjności akustycznej przy częstotliwościach poniżej 100 Hz, a także wysoką dźwiękoszczelność także przy średnich i dużych. Stropy w halach przemysłowych są na ogół wykonywane jako przegrody poziome ciężkie – z prefabrykowanych lub wylewanych płyt żelbetowych. Ze względów konstrukcyjnych ich grubość sięga powyżej kilkunastu centymetrów, w związku z czym charakteryzują się dużą izolacyjnością akustyczną, wynoszącą na ogół powyżej 50 dB. W przypadku konieczności zastosowania lekkich stropów, należy wykonywać je jako przegrody podwójne.
Przepisy krajowe niestety nie określają, jaką minimalną izolacyjność akustyczną powinny mieć przegrody w halach przemysłowych. Ich dźwiękoszczelność należy dobierać w taki sposób, aby obniżyć hałas na stanowiskach pracy do wartości określonych przepisami normatywnymi, przede wszystkim w rozporządzeniu Ministra Pracy i Polityki Socjalnej z dnia 6 czerwca 2014 r.
Dlatego na etapie projektowania warto skonsultować rodzaj zastosowanych przegród zewnętrznych i wewnętrznych z akustykiem. Obecnie hale przemysłowe są budowane z wykorzystaniem konstrukcji stalowych z obudową, tzn. ścianami, stropami, dachem, wykonanymi najczęściej w technologii lekkiej, np. z płyt warstwowych z rdzeniem termoizolacyjnym. Tego typu przegrody zazwyczaj zapewniają wystarczającą ochronę przeciwhałasową hali ze względu na emisję niepożądanego dźwięku do środowiska oraz dopuszczalne jego wartości na stanowisku pracy. Nie sprawdzają się jednak w sytuacji, gdy poziom hałasu sięga powyżej 85 dB(A) lub gdy wewnątrz hali potrzeba wydzielić obszar o podwyższonym komforcie akustycznym, tzn. niskim tle akustycznym. W takim przypadku jedynym rozwiązaniem jest stosowanie przegród ciężkich, np. murowanych, prefabrykowanych, wylewanych lub podwójnych. Szczególnie efektywne są te ostatnie, gdyż charakteryzują się dużą izolacyjnością akustyczną przy stosunkowo niedużej masie własnej.
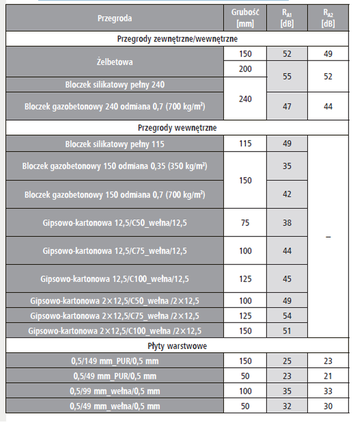
i
W przypadku hal przemysłu lekkiego, gdzie występuje hałas na poziomie 85 dB(A) lub mniejszy, przegrody z płyt warstwowych na ogół wystarczają, aby w dostateczny sposób ograniczyć jego emisję do środowiska. Natomiast za pomocą płyt warstwowych z rdzeniem z wełny mineralnej można wydzielać także zamknięte obszary wymagające pracy o zwiększonej koncentracji uwagi. Na przykład, stosując płyty warstwowe o izolacyjności RA1 = 35 dB (panele o gr. 10 cm z rdzeniem z wełny mineralnej) do budowy niedużych projektowo-administracyjnych pomieszczeń o kubaturze do 150 m3, hałas o poziomie 80 dB(A) można obniżyć do 42–45 dB(A), czyli do wartości wymaganych dla pokojów administracyjnych i biur projektowych. Niemniej jednak dźwięk o takim natężeniu jest wyraźnie słyszalny i, zdaniem autora, jest zdecydowanie za duży jak dla pomieszczeń wymagających intensywnej i produktywnej pracy umysłowej – nie powinien on przekraczać 35 dB(A). Dlatego przy wydzielaniu tego typu pomieszczeń w halach przemysłowych o typowych poziomach hałasu (80 dB(A)) należy stosować przegrody o izolacyjności akustycznej powyżej 42 dB (RA1 ≥ 42 dB).
Do budowy ścian wewnętrznych murowanych w halach przemysłowych mogą być wykorzystywane bloczki silikatowe o grubości powyżej 10 cm lub gazobetonowe o grubości ponad 15 cm, przy czym w przypadku tych drugich należy stosować odmianę o dużej gęstości (700 kg/m3). Niezwykle skutecznym i jednocześnie prostym rozwiązaniem jest wykonanie lekkiej zabudowy w systemie płyt gipsowo-kartonowych. W takim przypadku mamy do czynienia z przegrodą podwójną, która dzięki swojej konstrukcji, nawet przy stosunkowo niedużej masie ściany, zapewnia dużą izolacyjność akustyczną. Dobrą praktyką jest również stosowanie podwójnego płytowania ściany, np. z użyciem dwóch płyt gipsowo-kartonowych o gr. 12,5 mm z każdej strony przegrody.
Zwiększa to jej wytrzymałość mechaniczną, a także znacznie poprawia dźwiękoszczelność. Na przykład, ściana z podwójnym płytowaniem na profilach C75 charakteryzuje się o 10 dB większą izolacyjnością niż przegroda z płytowaniem pojedynczym. Należy także pamiętać o zastosowaniu w pustce powietrznej takich ścian podwójnych wyrobów dźwiękochłonnych, np. mat z wełny mineralnej, które znacznie poprawiają nie tylko izolacyjność termiczną, ale i akustyczną. Przy ich braku dźwiękoszczelność przegrody podwójnej spada nawet o 10 dB.
Izolacyjność akustyczna przegrody podwójnej jest znacznie większa niż panelu warstwowego w całym zakresie częstotliwości. Ponadto zastosowanie podwójnego płytowania zwiększa R ściany o 10 dB względem płytowania pojedynczego. Należy jednak zwrócić uwagę na to, że dźwiękoszczelność lekkich przegród podwójnych w zakresie małych częstotliwości jest stosunkowo nieduża.
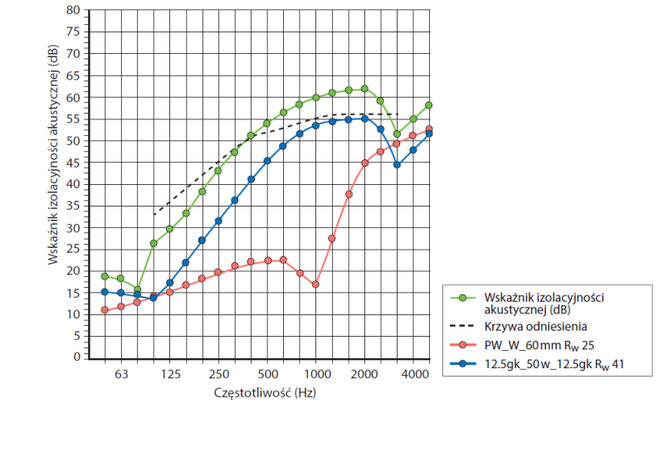
i