Spis treści
Dlaczego ciągłość produkcji jest tak ważna?
Mówiąc w dużym uproszczeniu: im mniej jest przerw w produkcji, tym więcej przedsiębiorstwo może wytworzyć produktów w danym czasie. Oczywiście jest to istotne przede wszystkim w przypadku przedsiębiorstw, które realizują produkcję wielkoseryjną. W obecnych czasach coraz częściej firmy produkują małe serie, a nawet prowadzą produkcję jednostkową. Wówczas przerwy w produkcji są nieodłącznym elementem dnia pracy w takiej fabryce. Konieczne są bowiem np. do przezbrojenia linii produkcyjnej, wprowadzenia nowego oprogramowania czy dostarczenia odpowiednich podzespołów do produkcji. Przerwy w produkcji często są również cyklicznie planowane, żeby móc przeprowadzić niezbędne czynności serwisowo-konserwacyjne, bez których długotrwałe użytkowanie maszyn czy urządzeń produkcyjnych będzie niemożliwe.
Problemem dla każdego przedsiębiorstwa produkcyjnego są naturalnie wszelkie niespodziewane przerwy w produkcji. Każdy taki postój może generować bowiem niepożądane straty lub inne negatywne konsekwencje.
Ciągłość produkcji ma przede wszystkim bezpośrednie przełożenie na wydajność zakładu, czyli wielkość produkcji w danej jednostce czasu. Nieplanowane przestoje mogą również być przyczyną opóźnień w realizacji zamówienia, co z kolei może przełożyć się na spadek zaufania klienta, jego mniejszą satysfakcję, a w skrajnym przypadku także jego utratą.
Przerwy w produkcji generują także dodatkowe koszty związane np. z utratą surowców czy innych materiałów, w których przypadku przerwa w produkcji oznacza konieczność ich utylizacji. Dodatkowe koszty mogą pojawić się również przy okazji ponownego uruchomienia linii produkcyjnej czy konkretnych maszyn. Nieplanowana przerwa w produkcji i będące jej następstwem opóźnienie może powodować również konieczność zapłaty kary umownej.
Przyczyny przerwania ciągłości produkcji i sposoby im zapobiegania
Nieplanowane przerwy w produkcji mogą być następstwem różnych czynników. Przy czym można wyodrębnić 3 podstawowe grupy tego typu czynników: związane ze złą organizacją procesu produkcyjnego, z problemami technicznymi i wynikające z błędów ludzkich. Na każdy jednak potencjalny problem można znaleźć jakieś sensowne rozwiązanie – mogą to być odpowiednie systemy, instalacje czy procedury postępowania w kryzysowych sytuacjach.
Złe planowanie produkcji
Bardzo duży wpływ na ciągłość procesów produkcyjnych ma odpowiednie zaplanowanie tych procesów. Im zakład produkcyjny jest większy i im bardziej rozbudowany jest proces produkcyjny, tym więcej może pojawić się problemów, które mogą skutkować przerwami w produkcji. Problemy mogą wynikać np. z występowania tzw. wąskich gardeł w linii produkcyjnej. Przykładem może być zaplanowanie bezpośredniej współpracy dwóch maszyn czy innych systemów produkcyjnych o różnym poziomie wydajności. W sytuacji, gdy jedna maszyna skończy już swoją część cyklu produkcyjnego, a druga nie będzie jeszcze gotowa do kontynuacji procesu, może pojawić się przestój. W dłuższej perspektywie taka sytuacja może odbić się na dużo mniejszej wydajności całego procesu.
Planowanie produkcji obejmuje również m.in. kwestie dostaw niezbędnych surowców i materiałów do produkcji, a także ustalenie harmonogramu przeglądów i czynności konserwacyjnych. Błędy na każdym z tych etapów mogą skutkować niespodziewanymi przerwami ciągłości produkcji.
Rozwiązanie: Przedsiębiorstwa mogą korzystać z systemów czy specjalistycznego oprogramowania do zarządzania produkcją, których celem jest pomoc w skutecznym i wydajnym zarządzaniu produkcją. Systemy takie pomagają dokładnie zaplanować poszczególne fazy produkcyjne i uwzględnić wszystkie aspekty projektu, minimalizując w ten sposób ryzyko wystąpienia błędów na każdym etapie. Firma powinna być również przygotowana na pojawienie się różnorodnych błędów produkcyjnych. Mając wypracowane odpowiednie procedury postępowania, można szybko wznowić produkcję i zredukować wielkość strat.
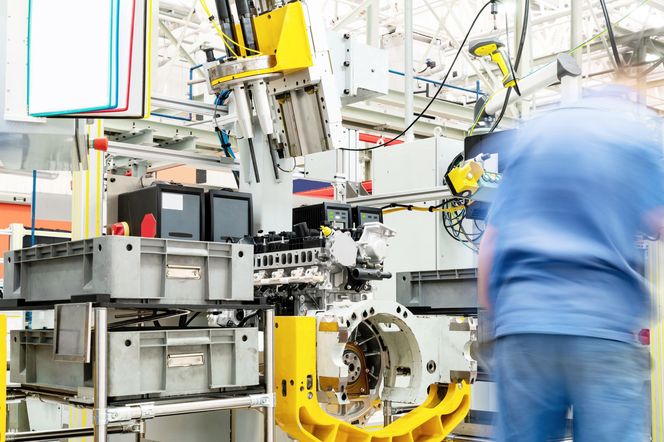
i
Awarie maszyn i urządzeń
Najczęściej przerwy w produkcji są następstwem awarii maszyn, urządzeń lub narzędzi, które biorą udział w procesie produkcyjnym. Mogą wynikać one z zużycia części, użycia złych części zamiennych, nieprawidłowej obsługi, błędów w oprogramowaniu, niewłaściwej konserwacji czy problemów z zasilaniem.
Rozwiązanie: Kluczowa w tym kontekście jest regularna konserwacja sprzętu produkcyjnego. Systematyczne przeglądy techniczne i serwis maszyn i urządzeń zapobiegają niespodziewanym awariom. Wykorzystując nowoczesne technologie, można wdrożyć tzw. konserwację predykcyjną, dzięki której można prognozować wystąpienie usterki i skutecznie jej zapobiegać. Awariom maszyn i urządzeń można również zapobiegać, zapewniając odpowiednie szkolenie pracownikom z obsługi tych narzędzi produkcji.
Problemy z dostawami/niedobór surowców
Równie częstą przyczyną przerwania ciągłości produkcji jest niedobór surowców i innych materiałów produkcyjnych, nieodpowiednia ich jakość albo opóźnienie w ich dostawie do hali produkcyjnej. Problemy te mogą wynikać z błędnego planowania procesu produkcyjnego i prognozowania niezbędnego zaopatrzenia, a także z nieodpowiedniego zarządzania zapasami. Ponadto może to być kwestia problemów logistycznych bądź intralogistycznych.
Rozwiązanie: Systemy do planowania zasobów przedsiębiorstwa ERP (enterprise resource planning) i planowania zapotrzebowania materiałowego MRS (material requirements planning), które pozwalają utrzymać odpowiedni poziom zapasów surowców i materiałów czy też części zamiennych.
Polecany artykuł:
Problemy z jakością
Przyczyną przestojów w produkcji mogą być również problemy z jakością wytwarzanych produktów, które mogą być następstwem błędów na etapie projektowania czy nieodpowiedniego nadzoru. Jeżeli udział wadliwych elementów lub niespełniających wymagań w produkowanej partii będzie zbyt duży, konieczne będzie przerwanie produkcji i wprowadzenie odpowiednich zmian związanych np. z oprogramowaniem linii produkcyjnej.
Rozwiązanie: Implementacja systemów monitorujących pracę maszyn i urządzeń oraz kontrolujących jakość wytwarzanych elementów (wykorzystująca najnowsze rozwiązania z obszaru Przemysłu 4.0, tj. narzędzia internetu rzeczy, sztuczną inteligencję czy analitykę dużych zbiorów danych) pozwala na szybkie wykrywanie nieprawidłowości i podjęcie odpowiednich działań.
Problemy z energią
Przerwy w dostawie prądu mogą skutecznie przerwać proces produkcyjny. Mogą być one następstwem braku zasilania na skutek awarii sieci energetycznej lub awarii infrastruktury technicznej.
Rozwiązanie: Typowym rozwiązaniem jest stosowanie systemów zasilania awaryjnego UPS lub awaryjnych generatorów prądu (agregaty prądotwórcze). Mają one przez określony czasu zapewnić zasilanie urządzeń produkcyjnych podczas przerw w dostawie prądu. W sytuacji, gdy mamy do czynienia z urządzeniami o kluczowym znaczeniu dla danego procesu i niezbędne jest niezawodne źródło zasilania, można stosować tzw. redundantne zasilanie awaryjne. Systemy redundantne polegają na tym, że energia może być dostarczana od dwóch różnych dostawców albo pochodzić z dwóch niezależnych od siebie źródeł.
Polecany artykuł:
Błędy ludzkie i niedobory kadrowe
Nieprawidłowa obsługa maszyn, ale również błędy w programowaniu czy błędne dobranie parametrów procesowych to typowe błędy ludzkie, które mogą powodować przerwy lub opóźnienia w procesie produkcyjnym. Bardzo często jest to efekt braku doświadczenia i niezbędnej wiedzy pracowników, które mogą wynikać z ogólnego braku wykwalifikowanej kadry czy chwilowych absencji.
Rozwiązanie: Regularne szkolenia pracowników z obsługi maszyn i urządzeń zwiększają efektywność pracy i minimalizują ryzyko błędów ludzkich. W przypadku braków kadrowych jedynym rozwiązaniem może okazać się wdrożenie automatycznych lub zrobotyzowanych systemów produkcyjnych. Roboty przemysłowe nie tylko mogą zastąpić człowieka w wielu czynnościach na linii produkcyjnej, ale wyróżniają się także większą efektywnością i mniejszą ilością błędów.
Ciągłość produkcji nie musi, ale może być kluczowym czynnikiem każdego przedsiębiorstwa produkcyjnego. Dzięki odpowiednim rozwiązaniom organizacyjnym i technologicznym można znacząco zminimalizować ryzyko przestojów produkcyjnych, a tym samym zwiększyć efektywność produkcji. Regularna konserwacja, szkolenia pracowników, systemy monitorowania czy plany działania w przypadku awarii to tylko niektóre z narzędzi, które pozwolą na osiągnięcie tego celu.
- Zobacz również: Top 10 największych fabryk na świecie