Spis treści
Coboty (od ang. cobots – collaborative robots) obecne są na rynku dopiero od końca pierwszej dekady XXI wieku. Według najnowszych statystyk Międzynarodowej Federacji Robotyki (World Robotics 2024), ich udział w globalnej robotyzacji wciąż pozostaje niewielki. W 2023 roku liczba nowych robotów współpracujących po raz pierwszy w historii publikacji tego raportu spadła – na całym świecie zainstalowano 57 tys. nowych cobotów, co oznaczało wynik o ok. 2% gorszy niż rok wcześniej. W 2017 roku udział cobotów w ogólnej liczbie nowych instalacji robotów przemysłowych wynosił 2,75%, podczas gdy w ostatnich dwóch latach oscyluje już wokół 10,5%.
Polecany artykuł:
Co to jest cobot?
W obecnych przepisach czy normach nie znajdziemy precyzyjnej definicji cobota, co tylko potwierdza, że zmieniająca się dynamicznie technologia wyprzedza zdecydowanie zmiany w prawie i różnych przepisach. Żeby jednak cobot mógł współpracować „ramię w ramię” z człowiekiem, musi spełniać kilka podstawowych warunków.
Kluczowe w tym kontekście jest właśnie słowo „współpraca”. Możliwość pracy w bezpośrednim sąsiedztwie człowieka, bez konieczności stawiania specjalnych wygrodzeń czy innych stref bezpieczeństwa, wymusza inną konstrukcję cobota. Nie tylko jest on sporo mniejszy od tradycyjnego robota, ale również nie może mieć żadnych ostrych krawędzi, a gniazdo robocze, w którym pracuje cobot, nie może mieć stref ściskających.
Robot współpracujący musi ponadto mieć wbudowane różne funkcje bezpieczeństwa, w tym np. ogranicznik siły, momentu, prędkości i przyspieszenia, a także czujniki, które wstrzymują całkowicie ruch robota w przypadku wystąpienia kolizji. Bezpieczeństwo może zwiększyć dodatkowo wyznaczenie wirtualnej przestrzeni bezpieczeństwa wokół niego, a także dokładne wytyczenie trajektorii, po której będzie się poruszać ramię cobota. Dzięki tym zabezpieczeniom, nawet gdyby doszło do kontaktu z człowiekiem, ryzyko odniesienia poważnych obrażeń jest zredukowane do minimum.
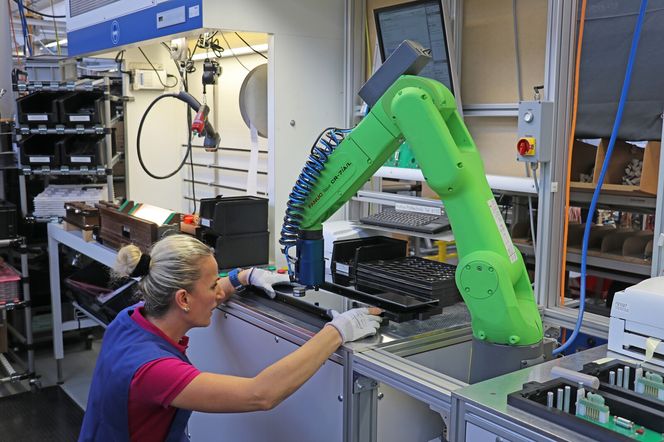
i
Cobot a tradycyjny robot przemysłowy – jakie są różnice?
Dużo większe i cięższe roboty przemysłowe wymagają często montażu na specjalnych fundamentach i zawsze powinny być odgrodzone do strefy, w której pracują ludzie. Coboty, z racji swoich dużo mniejszych gabarytów, zajmują mniej miejsca i są bardziej mobilne, przez co łatwiej można je przemieszczać pomiędzy różnymi stanowiskami.
Naturalnie tradycyjny robot jest dużo bardziej wydajny. Pracuje on z większą prędkością, sięgającą nawet 10 m/s, podczas gdy średni czas poruszania się cobota wynosi ok. 1 m/s. Zdarzają się sytuacje, w których robot współpracujący może rozwijać większą prędkość (do ok. 2,5 m/s), ale może pojawić się także konieczność ograniczenia maksymalnej prędkości do 50 mm/s (w przypadku np. przenoszenia przez cobota w sąsiedztwie człowieka przedmiotów o ostrych krawędziach). W efekcie standardowy czas cyklu pracy (np. w zadaniach typu pick and place) robota przemysłowego jest mniejszy niż sekunda, a dla cobota może już przekraczać 5 s.
- Przeczytaj również: Cyfrowy bliźniak czyli optymalizacja procesu projektowania w przedsiębiorstwie
Klasyczny robot to również sporo większy udźwig i zasięg ramion, choć nie ma tu jakiejś ściśle określonej granicy, która odróżniałaby cobota od tradycyjnego robota. Cobot może mieć niewielki zasięg ramienia, wynoszący kilkadziesiąt centymetrów, ale równie dobrze może sięgać po przedmioty oddalone nawet o 2 metry. Ponadto duży robot przemysłowy z reguły charakteryzuje się większą powtarzalnością i może realizować kompleksowo cały proces, podczas gdy cobot raczej będzie wykonywał mało złożone zadania.
Robota współpracującego dużo łatwiej natomiast można zaprogramować. Z reguły wystarczy do tego intuicyjny interfejs graficzny z dotykowym ekranem lub joystickiem. Możliwa jest także nauka poprzez prowadzenie ręczne. W większości przypadków wystarczy krótkie przeszkolenie, operator cobota nie musi być specjalistą IT. Inaczej natomiast wygląda proces programowania dużego robota, który do tego wykonuje bardziej skomplikowane czynności. Odbywa się on przy użyciu specjalistycznych narzędzi programistycznych, co oznacza konieczność zatrudnienia odpowiednio wykwalifikowanego programisty.
Polecany artykuł:
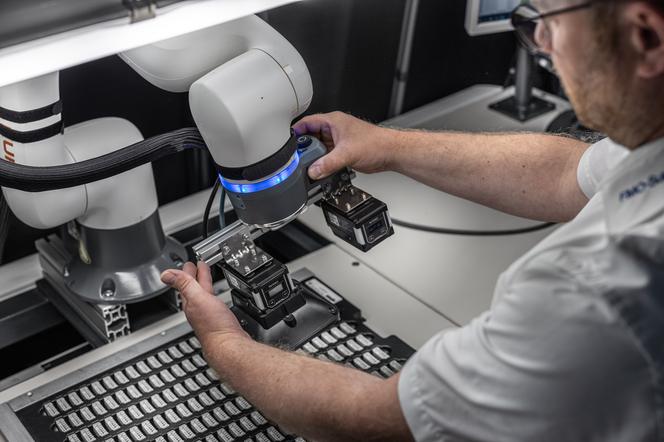
i
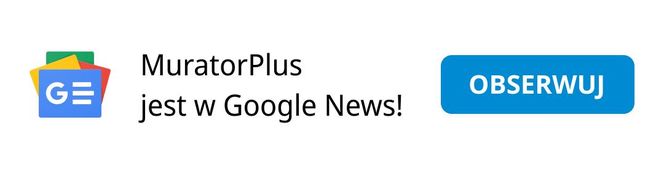
Jakie są korzyści z wdrożenia cobota?
Wspomniane kwestie bezpieczeństwa i brak konieczności stosowania dodatkowych wygrodzeń są bezsprzecznie największą korzyścią, jaką zapewnia wykorzystanie w zakładzie produkcyjnym robota współpracującego. Możliwość pracy w bliskim towarzystwie człowieka jest jednak tylko jednym z tego pozytywów. Stanowisko pracy cobota jest dzięki temu sporo mniejsze, co nabiera dodatkowego znaczenia w przypadku hal o małej powierzchni, a także tańsze w przygotowaniu.
Niewielkie rozmiary cobota pozwalają użyć go do zrobotyzowania takich obszarów, które właśnie ze względu na ograniczenia powierzchniowe nie mogły być zrobotyzowane. Stosunkowo lekkiego i niewielkiego cobota można też łatwo przenieść i zainstalować w innym miejscu w hali produkcyjnej. Łatwość jego programowania pozwala natomiast na częste zmiany wykonywanych przez niego czynności, dzięki temu cobot może wykonywać jakieś prace przy linii montażowe, by za chwilę obsługiwać jedną z maszyn. Wszystko to przekłada się na wzrost elastyczności produkcji, a więc szybsze reagowanie na zmieniające się zapotrzebowanie rynku.
Coboty są także proste w obsłudze i utrzymaniu, a ponadto są łatwe w konfiguracji i nie wymagają specjalistycznego programowania. Są więc idealne do tego, także dla małych i średnich firm, żeby rozpocząć proces automatyzacji przedsiębiorstwa.
Niższa cena samego cobota, brak konieczności zatrudniania wysoko wykwalifikowanych operatorów czy programistów, a także brak potrzeby stosowania dodatkowych zabezpieczeń sprawiają, że inwestycja w zakup robota współpracującego może zwrócić się dużo szybciej niż w przypadku tradycyjnego robota przemysłowego.
Wspomniane wcześniej ograniczenia sprawiają również, że coboty do pewnych zastosowań się jednak nie nadają albo będą dużo mniej wydajne od tradycyjnych robotów. Mniejszy udźwig i zasięg dyskwalifikują je od przenoszenia dużych i ciężkich przedmiotów na większe odległości. Mniejsza prędkość zmniejsza też wydajność wykonywanych przez nie niektórych prac, zwłaszcza przy produkcji wielkoseryjnej czy też zadaniach realizowanych na dużych konstrukcjach (np. malowanie lub spawanie).
Typowe zastosowania robota współpracującego
Coboty zyskują obecnie coraz bardziej na popularności i to bez względu na branżę. Sięgają po nie zarówno duże przedsiębiorstwa produkcyjne, jak i małe firmy. Możliwość podłączenia do ramienia cobota różnych efektorów końcowych powoduje, że są one wykorzystywane do wykonywania różnorodnych prac. Świetnie sprawdzają się m.in. przy wykonywaniu takich zadań jak podnoszenie i przemieszczanie przedmiotów, pakowanie i paletyzacja, obsługa maszyn (podawanie detali do obróbki i odbieranie gotowych elementów), spawanie, malowanie, polerowanie, klejenie, a także przy wszelkich pracach montażowych.
Rozwój w obszarze robotów współpracujących – zarówno jeśli chodzi o ich funkcjonalności, jak i parametry pracy – spowoduje, że zainteresowanie nimi będzie w dalszym ciągu rosło, a ich możliwości operacyjne będą się zwiększać. Coboty coraz częściej będą stanowić pierwszy krok do automatyzacji całych przedsiębiorstw lub poszczególnych procesów, zwłaszcza tych, które do tej pory postrzegano jako zbyt kosztowne lub skomplikowane.