Spis treści
Procesy logistyczne - dlaczego warto zautomatyzować?
Automatyzacja procesów logistycznych nie jest i nie może być celem samym w sobie, lecz jest koniecznością wynikającą z potrzeb klientów obsługiwanych przez dany magazyn, takich jak:
- terminowość,
- jakość,
- powtarzalność,
- obsługa spiętrzeń zamówień;
lub wiążącą się z potrzebami inwestora, np.:
- brak miejsca w istniejącym obiekcie,
- braki kadrowe i/lub zwiększające się koszty osobowe,
- wymagania technologiczne kooperantów,
- zamiar zwiększenia przepustowości magazynu,
- poprawa jakości i powtarzalności procesów,
- pewność stanu magazynowego,
- redukcja kosztów dystrybucji poprzez konsolidację w magazynie centralnym w zastępstwie wielu magazynów regionalnych.
Zapewne można znaleźć wiele innych powodów realizacji projektu automatyzacji magazynu, niemniej jednak decyzję o tym kroku warto przeanalizować wszechstronnie, w oparciu o własne doświadczenia zgromadzone w firmie lub z pomocą specjalistów od planowania procesów automatyzacji w celu opracowania projektu. Takie przygotowanie do inwestycji należy przeprowadzić przed podjęciem prac projektowych dotyczących przyszłego budynku.Osoby z branży budowlanej powinny zwrócić uwagę, iż procesy wewnątrzmagazynowe trzeba traktować jak cykle produkcyjne fabryk. Dlatego metoda planowania „od wewnątrz”, tj. od procesu do warunków zabudowy, a nie odwrotnie, jest zalecana w tego typu projektach.
Wielokrotnie spotykamy się w Polsce z praktyką budowania hal z przeznaczeniem magazynowym, które opierają się na cenowo optymalizowanych projektach deweloperów, które mają standardową wysokość czy dopuszczalne obciążenie posadzek przemysłowych. Prowadzenie prac przygotowawczych dla automatyzacji est w tym przypadku ciągłym poszukiwaniem kompromisu pomiędzy możliwościami urządzeń technologicznych i obiektu.
Niestety inwestorzy są często gotowi na optymalizację nakładów finansowych na budowę hali, nie uwzględniając późniejszych konsekwencji dla logistyki, co wiąże się ze stratą dla przyszłych kosztów operacyjnych magazynu.
Polecany artykuł:
Dobrze zaplanowany proces (łańcuch wszystkich procesów zazębiających się w obrębie jednego magazynu) z pomocą automatyzacji może prowadzić do wydatnej redukcji kosztów operacji logistycznej. Warunkami osiągnięcia tego celu są m.in.:
- wstępna ocena przepływów strumieni logistycznych z uwzględnieniem ekstrapolacji tej wielkości na najbliższe 3–7 lat przy jednoczesnym badaniu struktur zamówień i wynikających z tego parametrów, np. liczba sztuk/jedno pobranie z miejsca składowania,
- ustalenie warunków brzegowych budynku, takich jak wielkość powierzchni w oddzielnych strefach, wraz z ich wysokością (ważne przy wyznaczaniu współczynnika zagęszczenia magazynu w m³), rozstawem słupów nośnych i konstrukcji pomocniczych, nośnością posadzki, liczbą bram wjazdowych i wyjazdowych, określeniem klasy dopuszczalnego obciążenia ogniowego i/lub normy ppoż., dróg ewakuacji, rozmieszczeniem punktów sanitarnych, zabezpieczeniem zasilania energią itd.,
- planowanie przebiegu procesu logistycznego (łańcucha wszystkich następujących po sobie procesów) z uwzględnieniem natężenia strumienia i jego wydajności,
- synchronizacja wszystkich urządzeń i technologii zaplanowanych w projekcie, z uwzględnieniem dwóch kluczowych zasad planowania:– całkowita wydajność systemu jest taka, jak najsłabszego ogniwa,– każdy system mechanizacji procesu jest ograniczony przepustowością mechaniczną swoich komponentów,
- zaplanowanie rezerw procesowych i wydajnościowych na okresy spiętrzeń.
Jeśli spełni się te i wiele innych warunków dobrego planowania, można spróbować ocenić przyszłą efektywność procesową osiągniętą dzięki wprowadzeniu układów i systemów automatyzacji.Dobrym i praktycznym sposobem takiej weryfikacji (przed przystąpieniem do budowy) jest wyliczenie wskaźnika ROI dla projektu, przy świadomości teoretycznego jego znaczenia (dane wsadowe mogą ulec istotnemu wypaczeniu, np. wysokość wynagrodzeń lub wartości strumieni towarowych w przyszłości).
Niemniej jednak autor niniejszego artykułu chciałby zarekomendować jego sprawdzenie przy wprowadzaniu rozwiązań logistycznych w zakładzie, w celu wyznaczenia strategii i czynników mających wpływ na jej realizację.
Gdyby na zagadnienie wykonania projektu logistycznego spojrzeć także od strony budowlanej i włączyć aspekty kosztów wzniesienia obiektu, jego leasingu lub innej formy finansowania, to odpowiednimi wskaźnikami byłyby w tym przypadku NPV3 i IRR4.
Zalety automatyzacji
Z wieloletnich obserwacji autora wynika, że mogą nimi być:
- chęć kapitalizacji i wprowadzenia rozwiązań, które podniosą atrakcyjność obiektu dla potencjalnych kupców,
- chęć wyprzedzenia konkurentów rynkowych w celu otrzymania odpowiednich certyfikatów, zezwoleń czy dostępu do danej grupy produktowej (sytuacja często spotykana w branży farmaceutycznej).
Specyficzne wymagania branży stają się determinantą wprowadzenia automatyzacji w magazynach obsługujących:
- duże liczby zwrotów od klientów, np. sprzedaż odzieży online,
- krótkookresowe spiętrzenia godzinowe lub dniowe, np. farmacja, e-commerce towarów konsumpcyjnych i materiałów eksploatacyjnych w kanale sprzedaży B2B,
- dostawy do własnej sieci sprzedaży towarów wrażliwych, np. żywności.
Automatyzacja i mechanizacja mają jeszcze jedną zasadniczą zaletę, którą można spróbować nazwać „taktowaniem przepływu”, ponieważ wymuszają one działania pracowników oparte o ścisłą sekwencję w określonym tempie i z wysokim poziomem powtarzalności, co z kolei wpływa na poprawę jakości realizowanych zleceń poprzez wzrost wskaźników punktualności oraz zmniejszenie liczby uszkodzonych w transporcie przedmiotów.
Powtarzalność procesu logistycznego prowadzi także do podwyższenia wskaźnika dostępności, którym możemy określić „pewność” naszego biznesu lub, inaczej ujmując, poziom realizacji zleceń w stosunku do ich liczby podanej przez naszych odbiorców.
Jakie obszary można poddać procesowi automatyzacji?
W logistyce magazynowej zauważa się natomiast postęp technologiczny, pozwalający na wprowadzenie elementów automatyzacji praktycznie w każdym obszarze. Jedyne ograniczenie (warunek rozsądku) stanowi uzasadniony efekt ekonomiczny. Postęp w tej dziedzinie w Polsce jest równie dynamiczny i potęguje się wraz z narastaniem presji wynagrodzeń czy też braku rąk do pracy w magazynach.
Najczęściej elementy automatyzacji na krajowym rynku magazynów można spotkać w strefach składowania i kompletacji, sortowania oraz konsolidacji, a także pakowania. Już tych kilka obszarów wymienionych razem wskazuje wyraźnie na coraz większe znaczenie modelu biznesowego typu fulfillment i szeroko pojmowanego modelu e-commerce. W tego typu rozwiązaniach efektywność procesową osiąga się przede wszystkim poprzez mechanizację i automatyzację poniższych obszarów:
- kompletacji, np. przy zastosowaniu technologii pick-by-light, multi-order-picking, multi-level-picking i wsparcie ich mechanicznymi systemami składowania, takimi jak regały karuzelowe, układnice, shuttle itp.,
- sortowania,
- konsolidacji towarów pobranych (skompletowanych) w różnych strefach.
Wybór systemu automatyzacji
Wybór odpowiedniego systemu automatyzacji nie jest zagadnieniem, które można opisać na kilku stronach artykułu, poniżej przedstawiono jednak kilka podstawowych i kluczowych kryteriów doboru. Ale najpierw ważna uwaga: bez modelowania strumieni przepływu w przyjętym planie biznesowym na najbliższe 3–7 lat nie można odpowiedzialnie dokonać wyboru właściwego systemu automatyzacji.
Opierając się jedynie na zaleceniach lub reklamie dostawców, otrzymamy zespół urządzeń mechanicznych o nominalnej przepustowości mechanicznej, który przy założeniu idealnych i ciągłych warunków przepływu ma ją zagwarantować. W przeciwieństwie do niej mówimy o przepustowości logistycznej (rzeczywistej) wówczas, gdy dane urządzenie lub ich zespół, dzięki operacjom logistycznym na rzeczywistych zleceniach o zmiennej strukturze, jest w stanie z określonym stopniem dostępności7 dokonać obróbki danego strumienia towarowego. Przy wyborze systemu zalecane jest sprawdzenie następujących warunków brzegowych:
- budowlano-montażowe:
– wysokość zabudowy i strefy ochronne,– zapotrzebowanie na energię, powietrze, oświetlenie,– naciski na powierzchnię podłóg (posadzek, antresoli),– poziom hałasu,– sposób zabezpieczenia ppoż.;
- mechaniczne i procesowe:
– przepustowość mechaniczna i sprawdzona w testach przepustowość logistyczna,
– warunki ergonomii pracy na stanowiskach pracowników (wydajność długookresowa),– sposób łączenia z innymi systemami (zarówno mechaniczny, jak i ze strony IT),– dostępność części zamiennych i serwisowania,– możliwość modułowej rozbudowy bez konieczności wstrzymywania prac magazynu,– zgodność z normami, np. w zakresie zmienności natężenia prądu czy hałasu.Szereg innych warunków mogących zaburzyć ciągłość procesową w przyszłym magazynie ma istotny wpływ na wybór technologii, nie należy więc kierować się pojedynczymi parametrami technicznymi, a raczej porównywać wartości kilku przeliczników ekonomiczno-technicznych.
W tym miejscu autor chciałby przestrzec przed dokonywaniem wyboru poprzez stosowanie jedynie kryterium cenowego. Osobnym zagadnieniem jest infrastruktura sprzętowa i oprogramowanie. Już sama dostępność różnego typu oprogramowania, jego zdolności do parametryzowania i koszty obsługi powodują, że wybór właściwej konfiguracji staje się wyzwaniem nawet wówczas, gdy do pomocy zatrudnimy specjalistów.
Powodem jest przede wszystkim brak szerokiej bazy doświadczeń porównawczych i coraz to bardziej wymyślnych konfiguracji tego samego oprogramowania. W tej sytuacji dobre rozwiązanie stanowi przygotowanie specyfikacji procesowej oprogramowania przed ogłoszeniem przetargu oraz dokładna analiza realizowanych zadań i procesów.
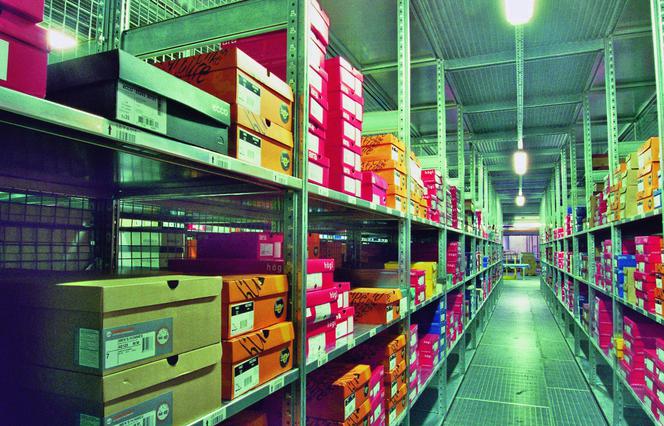
i
Przykłady automatyzacji, opisy urządzeń
Systemy regałowe do składowania i komplementacji
- Regały półkowe – służące składowaniu towarów o małej lub średniej rotacji, używane w układach rzędowych.
- Regały przepływowe – stosowane w magazynach kompletacyjnych opakowań pełnych lub pojedynczych sztuk pobranych bezpośrednio.
- Regały paletowe statyczne i przejezdne – przeznaczone do składowania dużych nośników logistycznych jak europalety; montowane w układach statycznych lub przejezdnych.
- Regały paletowe przepływowe – służące do składowania palet z towarami o dużej rotacji lub jako bufor konsolidacyjny gotowych zleceń.
- Regały paletowe kanałowe typu shuttle – stosowane przy składowaniu jednorodnego towaru z dużym współczynnikiem zagęszczenia w magazynie.
- Układy regałowe scalone – antresole.
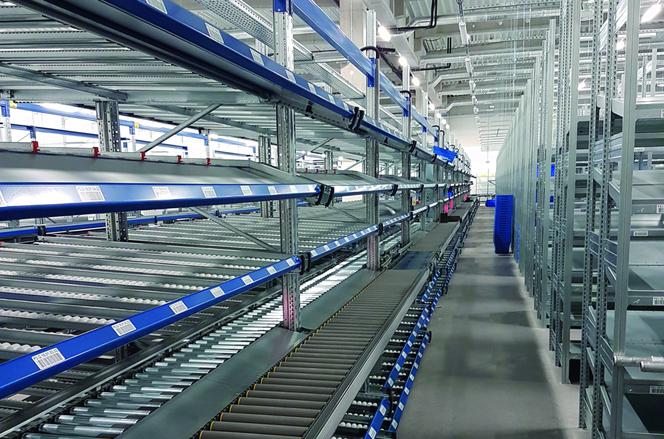
i
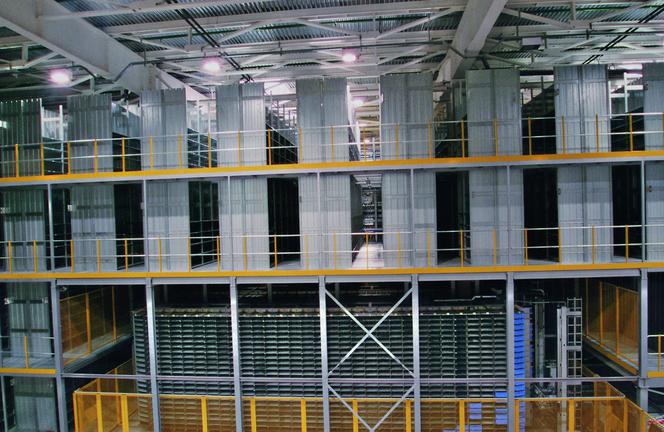
i
Urządzenia transportu wewnętrznego
- Przenośniki do pojemników i kartonów – rolkowe, pasowe, sekcyjne
- Przenośniki do palet – rolkowe i łańcuchowe.
- Układy szynowe – podwieszone i podłogowe.
- Układy samojezdne typu AVG (ang. Automated Guided Vehicle) – samodzielne pojazdy transportu podłogowego sterowane autonomicznie i bezkontaktowo, służące do transportu nośników logistycznych w magazynie (do pojemników i palet).
Urządzenia transportowo-odkładcze
- Układnice – urządzenia przemieszczające się wzdłuż dróg międzyregałowychw celu odkładania lub podejmowania jednostek ładunkowych z regałów. Ich konstrukcję nośną stanowi przejezdny słup lub rama, po której przemieszcza się wodzak. Wśród układnic wyróżnić można m.in. urządzenia typu Mini-Load do pojemników i kartonów czy AS/RS do palet.
Urządzenia magazynowo-komletacyjne (w układach lub samodzielne)System
- Shuttle – składa się ze specjalnej konstrukcji regałowej i ruchomej platformy. Urządzenie z własnym zasilaniem porusza się po szynach umieszczonych wzdłuż tuneli składowania, ładując i rozładowując palety. Startując z pozycji początkowej, platforma dokonuje załadunku/rozładunku bez żadnej pomocy z zewnątrz.
- Automatyczny regał karuzelowy – karuzele w układzie „towar do człowieka”, dostarczają artykuły bezpośrednio do rąk operatora, wykorzystując najkrótszą drogę transportową. Zasada działania polega na ruchu pionowym lub poziomym szeregowo połączonych półek.
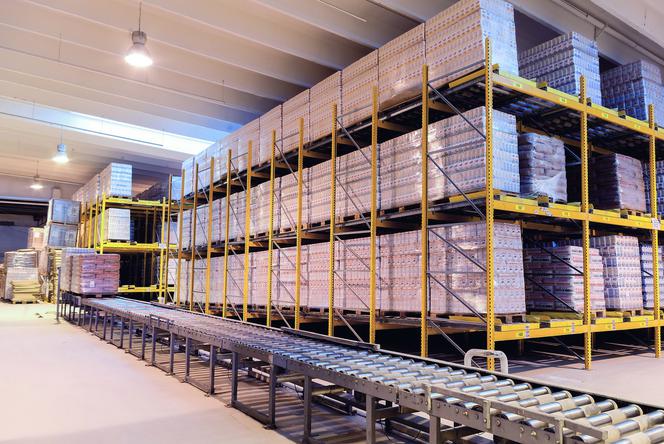
i
Wybór sposobu prowadzenia procesów logistycznych w nowo budowanym magazynie powinien zawsze opierać się z jednej strony na wytycznych pochodzących z analizy danych o przepływach, z drugiej zaś, na wyborze układu urządzeń gwarantujących najbardziej efektywny przebieg procesów, tj. o najlepszej zależności nakładu zasobów względem przemieszczenia lub obróbki.
Nakładanie na proces planowania ograniczeń wynikających z warunków istniejącej infrastruktury lub też planowanie jej bez wzięcia pod uwagę procesu logistycznego jest błędne i prowadzi do zwiększenia przyszłych kosztów operacyjnych w magazynie. Oszczędności poczynione podczas budowy obiektu spowodują podniesienie kosztów przeliczeniu na sztukę towaru lub przemieszczonej objętości.